Cutting down on CNC machining costs is a big deal for manufacturers who want to streamline their production and stay competitive. By using smart strategies and making careful decisions about Design and processes, you can save money without sacrificing the quality and performance of a CNC machined part. This guide explores practical ways to reduce CNC machining costs while meeting high-quality standards. Whether working on a small prototype or a big production run, these tips will help you make smart choices that save you money while getting the most out of CNC machining.

How to Calculate the Cost of CNC Machining
Calculating CNC machining costs involves several steps to determine the expenses of producing a specific part. Here’s a simplified breakdown of the process:
1. Gather Part Information:
Collect detailed information about the part, including its Design, dimensions, material specifications, tolerances, quantity required, and any special requirements.
2. Material Cost:
Determine the cost of the raw material needed for the part. This cost depends on the material type, size, and quantity.
3. CNC Tools’ Time Calculation:
Estimate the time it will take to machine the part. Break down the machining operations, and consider tool changes, CNC machine setup time, and machining duration for each operation.
4. Labor Cost:
Calculate the labor cost based on the hourly rate of machinists and operators setting up and operating the CNC machines.
5. Tooling Cost:
Estimate the cost of cutting tools, tool holders, and any specialized tooling required for the machining process.
6. Overhead and Facility Costs
Include overhead expenses like rent, utilities, maintenance, and administrative costs. Allocate these costs to the part based on machine usage time or labor hours.
7. Finishing and Post-Machining Costs:
Factor in any costs related to finishing processes, such as deburring, polishing, anodizing, or coating.
8. Markup and Profit:
Add a percentage markup to cover the profit margin and overhead costs of running the machining facility.
9. Shipping and Packaging:
If applicable, include the cost of packaging and shipping the finished parts.
10. Total Cost Calculation:
Sum up the material, machine time, labor, tooling, overhead, finishing, markup, and other applicable costs.
11. Cost per Part Calculation:
Divide the total cost by the number of parts produced to determine the cost per part.
Keep in mind that this is a simplified outline. The calculation might involve more detailed considerations and adjustments based on specific factors like machine capabilities, location, and supplier relationships. Additionally, using specialized software or tools for cost estimation can help automate and streamline the process, improving accuracy and efficiency. Collaborating with experienced CNC machining providers can also provide insights into cost-saving opportunities and accurate estimates for your project
What Influences the Cost of CNC Parts?
The cost of CNC parts is influenced by material selection, part complexity, machining time, tolerances, batch size, tooling, machine capabilities, finishing processes, labor costs, location, supplier relationships, design considerations, post-machining processes, quality control, regulatory compliance, market demand, and lead time requirements. Balancing these factors is essential to achieving cost-effective CNC machining while ensuring quality and functionality.
Tips for CNC Machining Cost Reduction
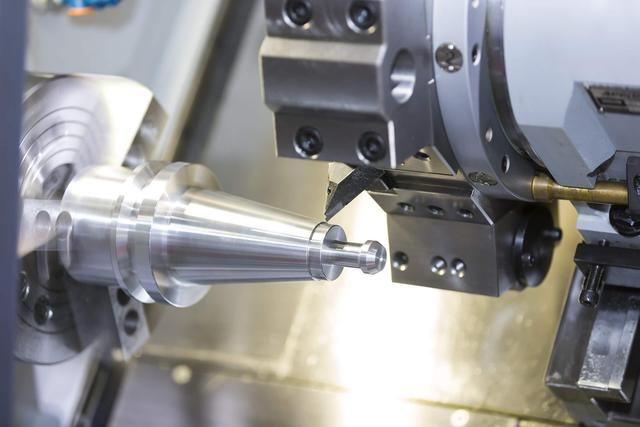
1. Simplify Design:
Minimize complex geometries and tight tolerances. Simpler designs are often faster and less expensive to machine.
A. Minimize Fillets:
Reduce the number of fillets and chamfers to simplify machining. Fewer fillets result in quicker machining. It involves opting for straight edges over filleted ones in components such as brackets, metal plates, housings, cover plates, and flanged parts. This design choice simplifies machining processes, reduces tool wear, and accelerates production, resulting in tangible cost savings while maintaining quality and functionality.
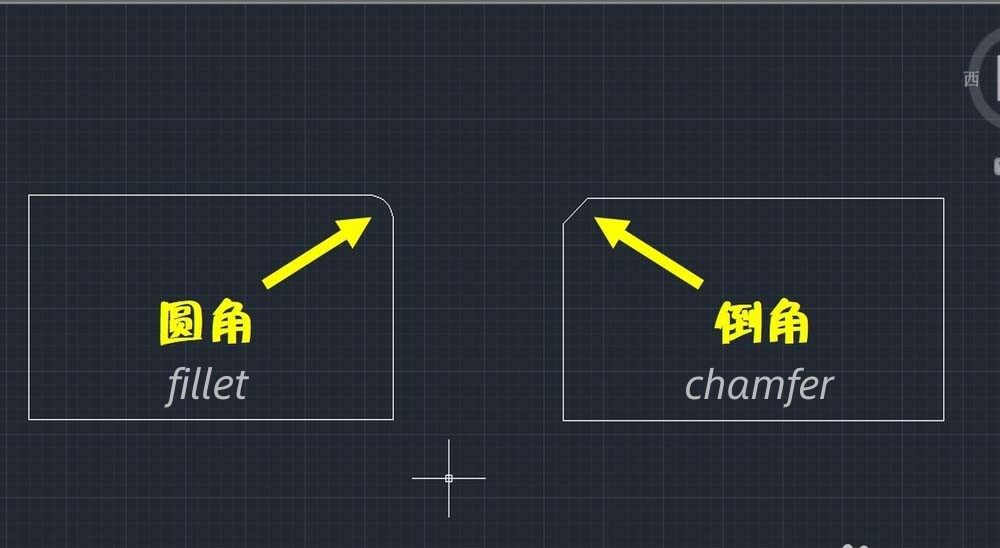
B. Avoid Overhangs:
“Avoid Overhangs” advises keeping part features from extending too far beyond their base, as this can make machining complicated and costly.
For example, a part with long arms sticking out might need extra support to avoid wobbling during machining. Similarly, parts with steep overhangs could need special tools to cut accurately. Following this advice helps make parts easier to machine, reducing the need for complex machine setups, extra supports, and special tools, which saves money during CNC machining.
C. Regular Patterns:
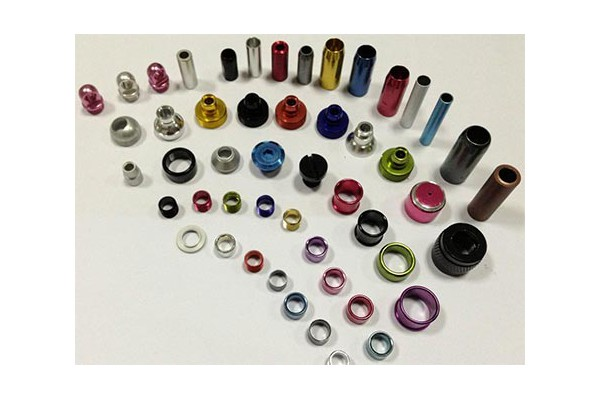
It means using consistent and repeating designs in part. This helps simplify CNC machining.
For example, a part with a grid pattern is easier to machine. Symmetry, in part, also makes machining simpler. Using these patterns helps tools move smoothly, improves accuracy, and saves time, reducing CNC manufacturing costs.
D. Enhance Symmetry:

Include mirrored features that need the same machining process, reducing separate setups.
Design parts that can be machined from both sides, reducing setup requirements.
E. Limit Cutouts and Pockets:
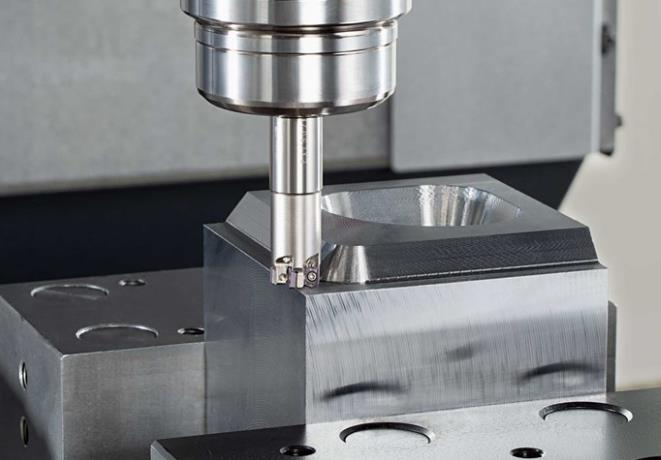
Use standard hole sizes to avoid custom tooling and simplify machining.
Design parts with shallow pockets for faster machining.
F. Standardize Shapes:
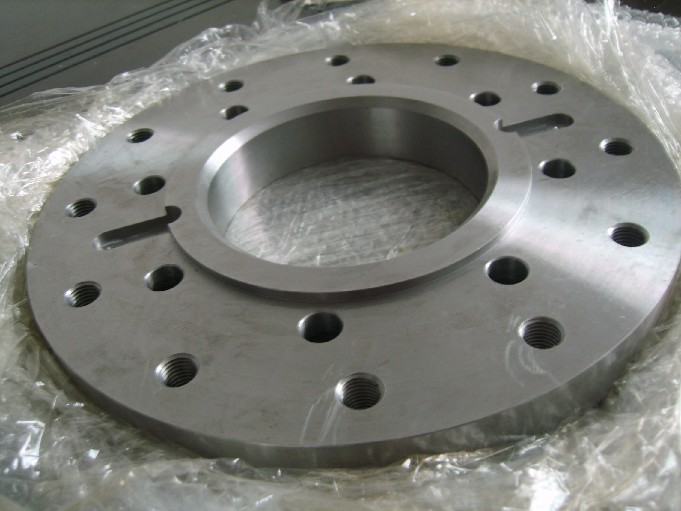
Design parts with simple bosses or protrusions. Complex boss shapes can increase machining time.
Ensure uniform wall thickness throughout the part to simplify machining. Better avoid the thin walls for easy machining.
G. Consolidate Features:
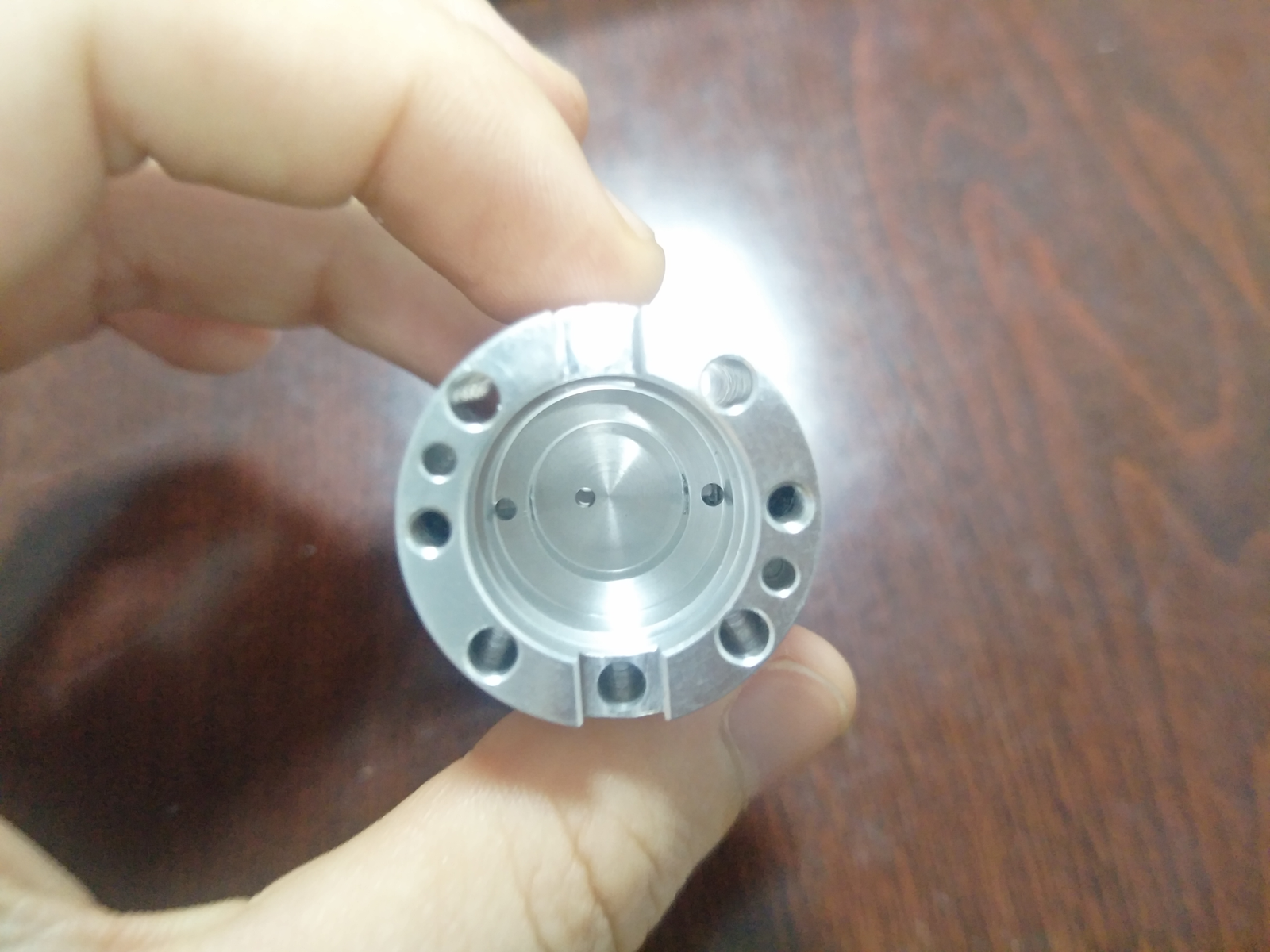
Use standard thread sizes or integrate threads into the Design to avoid additional machining steps.
Combine similar features like holes of the same diameter to reduce tool changes.
H. Minimize Detail Complexity:
Analyze for redundant or unnecessary features that can be removed without affecting function.
Focus on features contributing to functionality, reducing unnecessary complexity.
I. Design for Single Setup:
Design parts for single-sided machining to avoid flipping or repositioning during machining.
Minimize or eliminate undercuts requiring specialized tooling or additional setups.
J. Simplify Details:
Choose simpler geometries over complex shapes, reducing machining time.
Opt for straightforward angles and curves that are easier to machine.
K. Efficient Surface Finish:
Select surface finishes that achieve desired aesthetics without excessive complexity.
Avoid intricate surface patterns that demand complicated machining processes.
L. Function-Driven Design:
Prioritize features directly contributing to the part’s function, minimizing unnecessary complexity.
Eliminate non-essential design elements that don’t impact the part’s performance.
By incorporating these strategies, represented by alphabetical numbering, you can effectively simplify the Design of CNC machined parts, leading to streamlined manufacturing processes and cost savings.
2. Material Selection:
Opt for cost-effective materials that still meet your project’s requirements. Avoid exotic or high-cost materials unless essential.
3. Tolerances:
Specify tolerances only as tight as necessary. Looser tolerances can reduce machining time and complexity.
4. Batch Size:
Produce parts in larger batches to benefit from economies of scale and spread setup costs.
5. Optimize Tool Paths:
Use CAM software to generate efficient tool paths that minimize unnecessary movements and tool changes.
6. Minimize Manual Interventions:
Reduce the need for manual adjustments, tool changes, and repositioning during machining.
7. Efficient Nesting:
Arrange parts on the raw material to minimize waste and maximize material utilization.
8. Standard Tooling:
Design parts that can be machined using readily available cutting tools to avoid custom tooling costs.
9. Part Consolidation:
Combine multiple components into a single part to reduce machining steps and assembly costs.
10. Consider 3D Printing:
For prototypes or certain parts, consider additive manufacturing methods like 3D Printing, which can be cost-effective for lower quantities.
11. Design for Manufacturability (DFM):
Involve machinists early in the design process to ensure parts are optimized for efficient machining.
12. Material Efficiency:
Design with minimal waste in mind to avoid excessive material usage and cost.
13. Supplier Collaboration:
Work closely with your CNC machining provider to explore cost-saving opportunities and gather their insights.
14. Post-Machining Processes:
Design parts that require minimal post-machining processes, such as deburring or finishing.
15. Automated Inspection:
Use automated inspection methods to reduce manual inspection time and costs.
16. Optimal Finishing:
Choose surface finishes that meet your requirements without overdoing them, as intricate finishes can add costs.
17. Evaluate Prototypes:
Consider rapid prototyping before committing to full-scale CNC machining to refine designs and save costs.
18. Continuous Improvement:
Regularly assess and refine your processes based on cost-saving feedback and lessons learned.
19. Shipping Efficiency:
Optimize packaging and shipping methods to reduce associated expenses.

Conclusion:
In summary, lowering CNC machining costs involves simplifying Design, optimizing processes, and collaborating effectively. Manufacturers can achieve cost savings without compromising quality by focusing on design efficiency, minimizing material costs, and leveraging automation. Continuous improvement and close supplier relationships further enhance cost-effective CNC machining.