Introduction
Hardened steel is a formidable material known for its exceptional strength, durability, and resistance to wear and tear. It is extensively used in various industries, including automotive, aerospace, and tool manufacturing. However, machining hardened steel presents unique challenges due to its high hardness and toughness. To overcome these challenges and unlock the potential of hardened steel, advanced machining solutions machine machining of hardened steel have been developed. In this article, we will explore these hardened steel machining solutions and how they have revolutionized the machining of hardened steel.
Challenges in Machining Hardened Steel
Hardened steel is a strong and durable material known for its resistance to wear and tear. However, it poses challenges in machining and milling tools due to its extreme hardness and toughness. This paragraph will discuss the various materials, key tools, and challenges encountered when machining hardened steel.

Extreme Hardness: Steel that has been hardened usually has a Rockwell hardness rating of 50 or more. This hardness level makes it much stronger than materials commonly used for machining, like mild steel or aluminum. However, this high hardness can also cause tools to wear out quickly, making it challenging to achieve precise cuts and keep the tools sharp.
Heat Generation: When machining hardened steel, the friction between the cutting tool and workpiece material causes significant heat. This can result in various problems, such as tool wear, workpiece deformation, and changes in the workpiece material and properties. It’s essential to manage this heat to ensure successful machining.
Tool Wear: Hardened steel can cause tools to wear out quickly due to its abrasive nature and superior wear resistance. This material’s hardness can quickly degrade a tool’s cutting edge, leading to decreased machining efficiency and higher production costs. Frequent tool changes and sharpening may be necessary.
Surface Finish: Obtaining a smooth machined surface finish on hardened steel can be difficult. The steel’s hardness can result in uneven surfaces and the development of unwanted protrusions, which could necessitate further finishing procedures such as ceramic tools such as grinding or honing to obtain the desired surface texture.
Residual Stress: Machining hardened steel parts can introduce residual stresses that affect the part’s dimensional stability, requiring post-machining stress relief processes.
Chip Formation: When machining hardened steel, it’s important to be aware of potential chip breakage due to its hardness. This can lead to issues with tool wear and surface finish, so taking proper precautions during the machining process is important.
Machine Wear: When working with hardened steel, it’s important to note that the abrasive nature of this material and cutting temperature can cause significant wear and tear on your machining equipment. The cutting temperature and high forces involved in the cutting process can accelerate the wear of machine components like tool holders, spindle bearings, and way surfaces. To ensure your equipment remains in top condition, it’s crucial to take extra care when working with hardened steel and to monitor your machinery regularly for signs of wear.
Tool Selection: Choosing the right cutting tools for machining hard-turning hardened steels is crucial. Traditional tool materials may not be suitable for turning hardened steel, and specialized tool materials like cubic boron nitride (CBN) or polycrystalline diamond (PCD) are often required, which can be expensive.
Coolant and Lubrication: To ensure optimal machining performance and prolong tool life, it is important to maintain proper cooling and lubrication. The machining quality can be compromised without sufficient coolant and lubricant, and tool life can be significantly reduced.
Safety Considerations: Machining hardened steels can lead to high cutting forces and tool breakage. It is crucial to implement safety measures, such as machine guarding and personal protective equipment, to ensure the safety of operators and equipment.
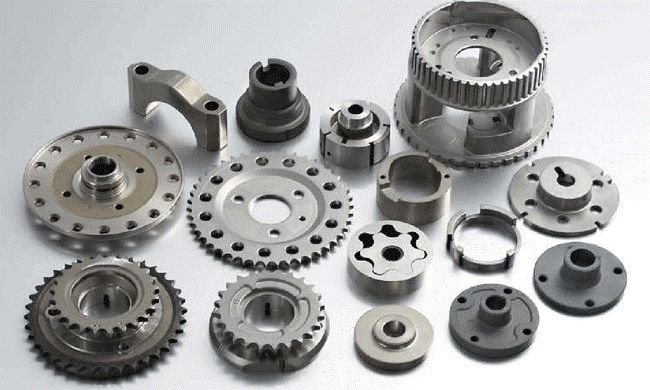
Innovative Machining Solutions
Machining hardened steel has always been challenging because of its exceptional hardness and durability. Fortunately, with the continuous advancements in technology and engineering, innovative machining solutions have emerged to overcome these challenges and enable efficient and precise machining of hardened steel. This has made it easier for manufacturers to manufacture machine-hardened steel more accurately and precisely.

Advanced Tool Materials: The task can be pretty challenging when machining hardened steel. Traditional tool materials like high-speed steel (HSS) or carbide are not equipped to handle the extreme hardness of hardened steel, which can cause difficulties in high cutting speeds. However, there are new tool materials available now that have been specifically designed to tackle this problem. Cubic boron nitride (CBN) and polycrystalline diamond (PCD) are two such materials that offer superior hardness and durability. These advanced materials maintain their sharpness for longer periods, which helps to improve tool life, cutting force, and machining efficiency.
Cutting Tool Coatings: It is now standard practice to apply specialized coating materials on cutting tools when machining hardened steel. Coatings such as titanium nitride (TiN), titanium carbonitride (TiCN), and diamond-like carbon (DLC) coating are commonly used to extend tool lifespan and decrease friction, thereby reducing heat buildup during machining. Moreover, these coatings enhance chip evacuation, providing a more seamless cutting process.
Coolant and Lubrication Systems: Proper coolant and lubrication systems are essential for handling the heat produced during machining. Advanced lubricants and high-pressure coolant systems work together to effectively reduce tool wear, dissipate heat, and improve the evacuation of chips. These systems maintain the workpiece’s dimensional stability and surface finish.
High-Speed Machining: One effective method for cutting edge geometry while reducing the time spent on workpieces and minimizing heat generation is high-speed machining. This involves increasing cutting speed and using lighter feeds, which can be even more effective when combined with advanced tool materials and coatings.
Cryogenic Machining: Cryogenic machining is a cutting-edge technique that involves cooling the cutting tool to extremely low temperatures using liquid nitrogen. This process dramatically reduces heat generation during machining, prolonging tool life and improving surface finish. It also reduces the wear resistance and the risk of thermal distortion in the workpiece.
Adaptive Machining: During the machining process, adaptive technologies like real-time monitoring and tool wear detection enable adjustments, which minimize tool wear and maximize tool life, leading to consistent product quality, long tool life, and reduced production costs.
Post-Machining Processes: Techniques such as grinding, honing, and superfinishing can achieve the desired surface finish and dimensional accuracy, ensuring the final product meets stringent quality standards. Additionally, advanced machining offers numerous benefits. Several techniques can be utilized to achieve the desired surface finish and dimensional accuracy to meet strict quality standards. These techniques include grinding, honing, and superfinishing. Moreover, advanced machining provides numerous advantages.
Benefits of Advanced Machining Solutions
Adopting advanced machining solutions has revolutionized the way hardened steel is machined, offering many benefits to manufacturers. These innovative approaches have addressed the unique challenges of hardened steel machining and have significantly improved efficiency, precision, and cost-effectiveness.
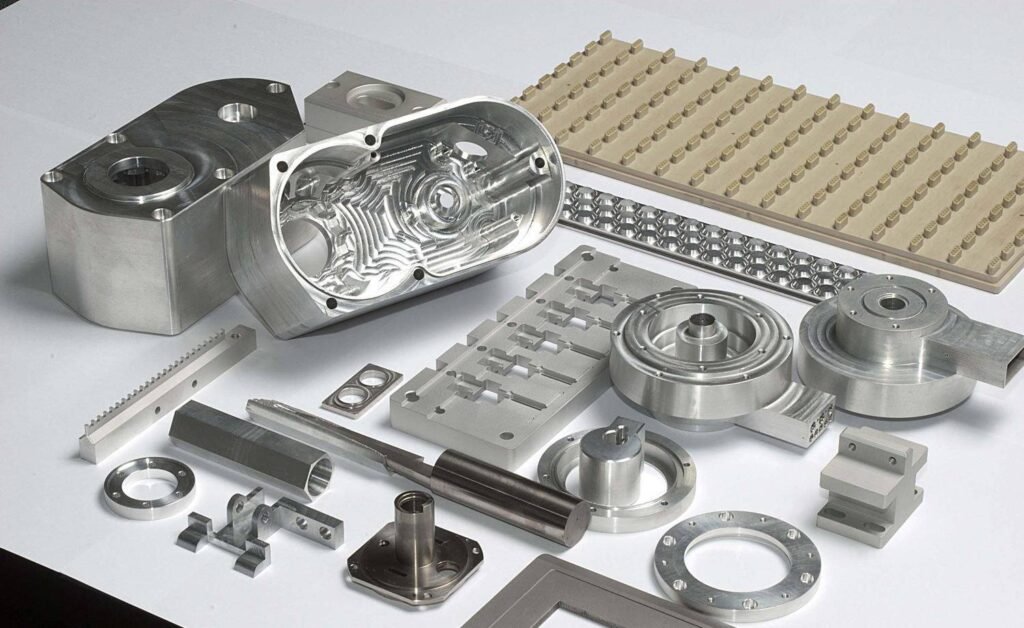
Increased Efficiency: By implementing advanced machining and coating solutions, manufacturers can improve their productivity and efficiency. Using specialized tool materials such as cubic boron nitride (CBN) and polycrystalline diamond (PCD), along with cutting-edge coatings, can significantly extend tool life. This reduces downtime for tool material changes and produces more parts in less time.
Improved Surface Finish: In various industries, attaining a top-notch machined surface finish on hardened steel parts is crucial. Using sophisticated techniques, such as specialized tool coatings and precise cooling systems, yields a smoother surface finish. As a result, the requirement for laborious and expensive secondary finishing processes, like grinding and polishing, is reduced.
Enhanced Precision and Consistency: Utilizing advanced machining techniques leads to accurate and reliable machining, allowing for high-speed cutting and the consistent production of parts that meet strict tolerances and exact specifications.
Cost Savings: Manufacturers can save a lot of money by extending the life of their tools and reducing wear and tear. By replacing tools less frequently, they can cut down on tool expenses, save on labor costs related to tool changes, and reduce the time their machines are out of commission. Additionally, reducing the need for secondary finishing processes can help save time and resources.
Reduced Heat Generation: To treat heat and prevent tool wear and workpiece deformation caused by heat, it’s essential to have efficient heat treatment, coolant, and lubrication systems in place. Incorporating cryogenic and high-speed machining techniques can also help manage heat generation and prolong tool life.
Enhanced Safety: Improved tool life and reduced wear contribute to a safer machining environment. Fewer tool changes mean fewer opportunities for tool-related accidents. Moreover, advanced monitoring and tool wear detection systems enhance overall safety by providing real-time insights into the machining process.
Optimized Material Utilization: Longer tool life and improved precision allow manufacturers to maximize material utilization. This is especially important when working with expensive or hard-to-source materials like hardened steel, as it reduces material waste and associated costs.
Competitive Advantage: Adopting advanced machining solutions gives manufacturers a competitive edge. The ability to produce high-quality hardened steel components efficiently and cost-effectively positions companies as leaders in their respective industries, attracting more customers and business opportunities.

Conclusion
Machining hardened steel is no longer an insurmountable challenge, thanks to the development of advanced machining solutions. These solutions, from cutting tool materials and coatings to innovative cooling techniques and adaptive machining technologies, have transformed how manufacturers approach steel machining. With improved efficiency, precision, and cost-effectiveness, these solutions are driving advancements in industries that rely on the strength and durability of machining hardened steels and steel components. As technology evolves, we can expect even more innovative solutions to emerge, further expanding the possibilities for machining this formidable material.
This concludes our introduction. Please consider sharing it with your colleagues and peers if you find it valuable. To delve deeper into CNC and machining capabilities, consider subscribing for further insights. Should you encounter any precision machining requirements or related challenges, STCNC stands ready to assist you in finding solutions.