Introduction
In modern manufacturing, the widespread use of CNC (computer numerical control) technology has made CNC mechanics and CNC programmers indispensable in the manufacturing process. Precision machining plays a crucial role in ensuring the accuracy and quality of the products manufactured. Although they contain “CNC” in their job title, their functional and technical requirements differ significantly. Here’s a closer look at the differences between the two roles.
What is the difference between a CNC machinist and a programmer?
In the manufacturing industry, understanding the machining process is crucial. Machinists must be comfortable with systems and understand the code, but a programmer must have an in-depth understanding of how to write code. CNC machinists often use machining centers to perform their tasks. Each role requires specific technical skills; machinists must be adept with various systems, while programmers must be proficient in different programming languages and technical drawings.
CNC Machinist
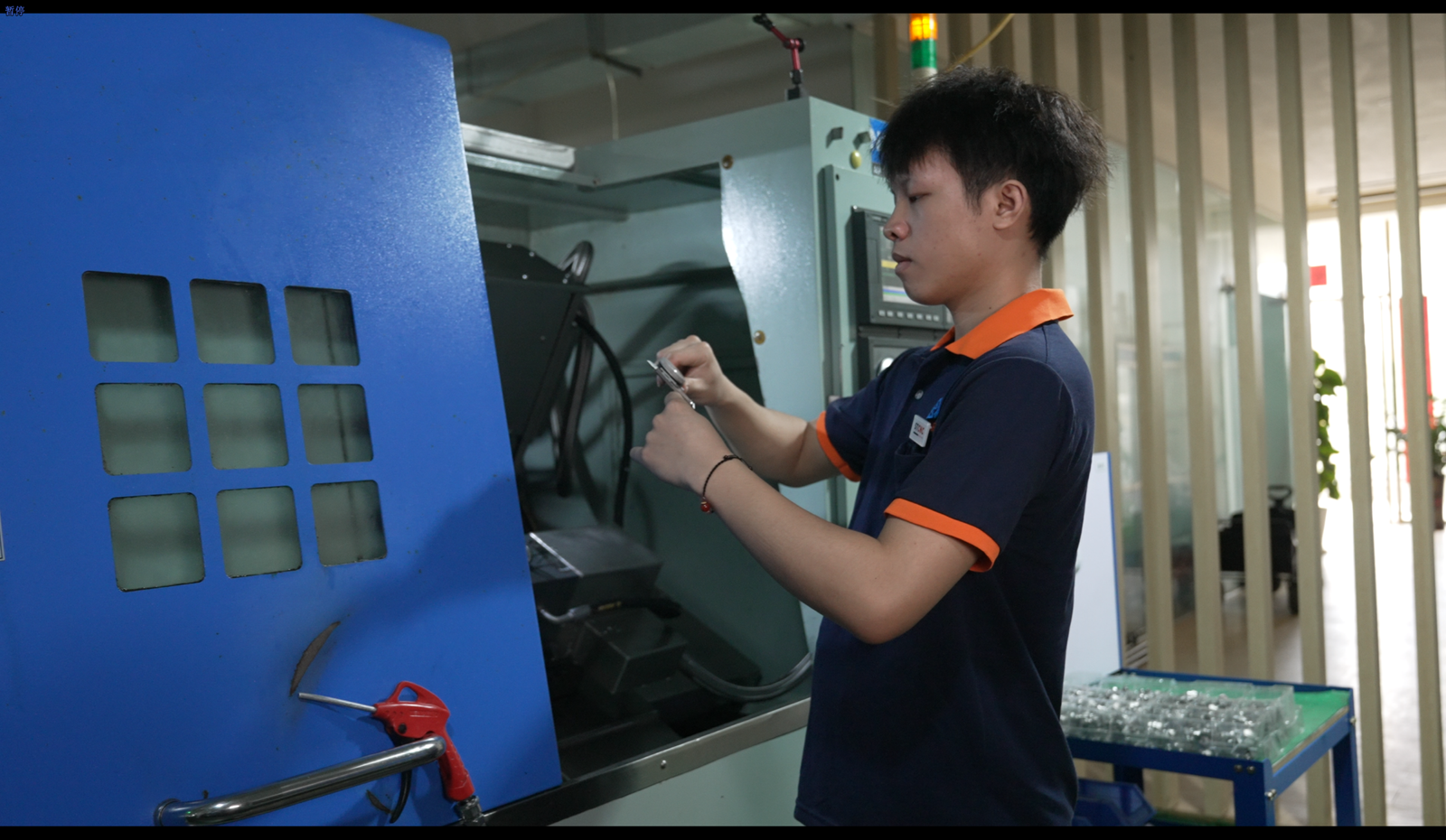
CNC machinists are operational experts in the machining process, responsible for the operation of CNC machines and cutting tools and monitoring the quality and efficiency of the machining processes. They frequently use machining centers to perform their tasks. Their primary responsibilities include:
Machine operation and setup
Skilled operation of various CNC machine tools, such as milling machines, lathes, drilling machines, etc., using cutting tools according to product requirements to set machine parameters and working fixtures. Machining centers are also utilized to enhance precision and efficiency in the manufacturing process.
Process control
Responsible for loading raw materials, running machining procedures, and monitoring dimensions, surface quality, and machining parameters.
Quality assurance and adjustment
During the process, make necessary adjustments and corrections to ensure the finished product meets the design specifications, tolerances, and quality standards.
Safety and Maintenance
Ensure the safety of the operation process and regularly carry out preventive maintenance and maintenance of the machine to ensure the stability of the equipment and long-term operation effect.
CNC Programmer
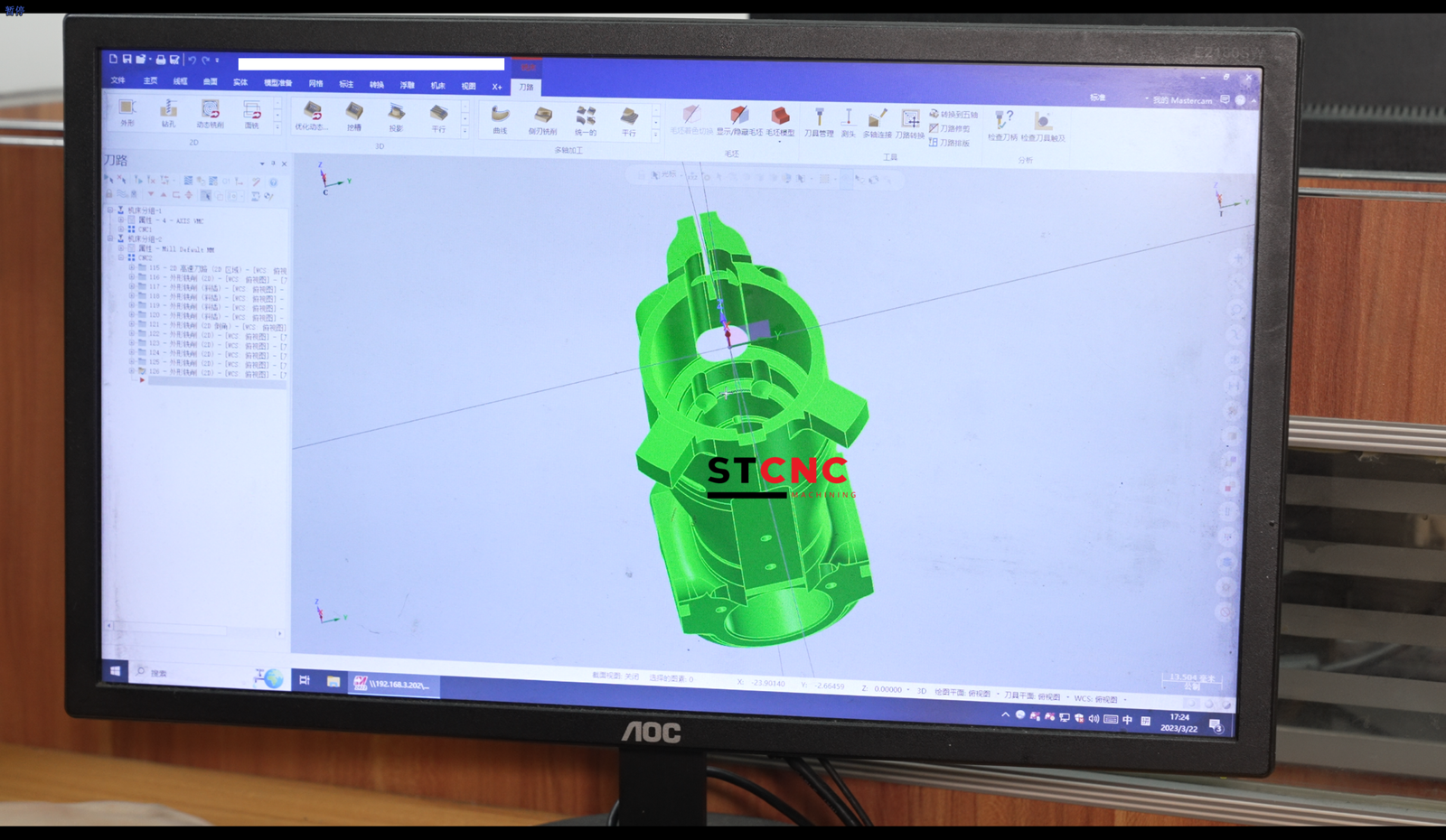
CNC programmers focus more on developing and optimizing CNC machining procedures, including optimizing tool paths, for more efficient, precise, and automated production within the machining process, requiring a solid mechanical aptitude. They also use G-code to control and automate the machining process. Their duties include:
CAD/CAM Software Applications
Proficient in CAD (Computer Aided Design) and CAM (Computer Aided Manufacturing) software, able to generate machine instructions from design drawings.
Program writing and debugging
Write and debug a CNC machining program according to product design requirements, including G-code for optimizing the cutting path, tool path, and machining sequence.
Process optimization
Through technical analysis and process optimization, processing efficiency and product quality can be improved, cycle time can be reduced, and scrap rate and production cycle can be lower.
Technical support and Training
Provide technical support to CNC machinists, solved machining challenges, and conducted necessary operation training and guidance.
Contact between CNC mechanic and CNC programmer
Program delivery and understanding
Programmer programming: CNC programmers write machining programs according to design drawings and process requirements to ensure accuracy and execution.
Machinists receive programs: CNC machinists receive programs, understand machining steps and requirements, and load and run programs on the machine.
Feedback and optimization
Mechanic feedback: In the actual operation process, CNC mechanics will find feedback on machining problems, such as dimensional deviations, surface quality problems, etc.
Programmer optimization: Based on feedback from mechanics, CNC programmers adjust and optimize programs to improve machining paths and process parameters.
Technical support and Training
Programmer Support: CNC programmers provide technical support to CNC mechanics, answer questions in operation, and help solve complex technical problems.
Mechanic Training: Programmers train mechanics to improve their operational skills and understanding of procedures, ensuring they can perform machining tasks efficiently.
Work together
Common goal: CNC operators, CNC mechanics, and CNC programmers work together in the machining process to ensure product quality and productivity. Their collaborative relationship is not only about the execution and feedback of tasks but also about solving challenges and problems in production together to enhance production efficiency.
What skills are required to become a CNC machine operator?
In order to become the most effective CNC operator, one must possess strong technical knowledge and be well-versed in the computer programming languages CAD/CAM. One must also have solid mathematical skills, especially in geometry and triangulation. Mechanical abilities, detail, and the ability to diagnose mechanical issues are essential.
Technical skill
Machine tool operation skills:
Skilled operation of various types of CNC machine tools, such as milling machines, lathes, and grinders, requires proficiency in machining techniques. One must also understand the operation flow and characteristics of different machine tools.
Programming Basics:
Although writing complex programs is unnecessary, basic knowledge of G and M code is. Learn how to input and modify simple processing programs.
Measurement and inspection skills:
Ability to use various measuring tools such as vernier calipers, micrometers, and altimeters for dimensional inspection and quality control of parts.
Material knowledge:
Understand the processing characteristics of different materials (such as metal and plastic) and select the appropriate cutting tools and cutting parameters
Cognitive skill
Problem-solving skills:
Ability to identify and resolve machining issues such as dimensional deviations, tool wear, and surface quality issues, requiring strong analytical skills.
In detail:
A high level of attention and care ensures that every processing step is according to the specifications and avoids errors.
Time Management:
Manage time effectively, arrange processing tasks reasonably, and improve production efficiency.
Soft skills
Communication skills:
Good interpersonal skills to communicate effectively with CNC programmers, engineers, and colleagues to ensure accurate information is conveyed.
Teamwork:
Ability to work with team members to solve problems and improve productivity.
Adaptability:
Adapt to different working environments and task changes and flexibly respond to various challenges.
Safety awareness
Safe operation procedures:
To ensure the safety of yourself and your colleagues, familiarize yourself with and strictly follow the factory’s safety protfactory’s safe operation procedures.
Protective measures:
Use personal protective equipment (PPE), such as safety glasses, gloves, and protective clothing.
Learning ability
Continuous learning:
Maintain an interest in new technologies and equipment, and actively participate in Training and learning to upgrade your skill level through continuous improvement.
Technical update:
Keep abreast of the latest CNC technologies and processes and constantly improve your working methods.
Practical experience
Internship and Training:
Gain practical experience through hands-on Training and internships, and become familiar with machine tools and machining methods.
Field operation:
Gain experience in natural production environments to deal with various operational issues and challenges.
Conclusion
In a CNC environment, the roles of CNC Machinists and CNC Programmers are distinct yet deeply interconnected within the machining process. CNC Machinists are the hands-on operators who bring the machining programs to life, while CNC Programmers are the technical experts who create and optimize these programs. Their collaboration and continuous interaction are vital for ensuring high-quality production and operational efficiency. By understanding and respecting the unique contributions of each role, manufacturing companies can better allocate resources, streamline processes, and stay competitive in a dynamic market.