Threads are one of the standard geometric features in mechanical engineering and have widespread applications. There are various machining processes for threads, such as rolling and chasing based on plastic deformation and turning, milling, tapping, thread grinding, and thread lapping based on cutting. Thread turning is one of the most commonly used single-piece or small-batch production methods. As a fundamental function of CNC lathes, thread-turning machining can encounter various issues. Today, I will share some common problems and solutions when turning threads on CNC lathes, focusing on the challenges and solutions associated with cnc turning thread operations.
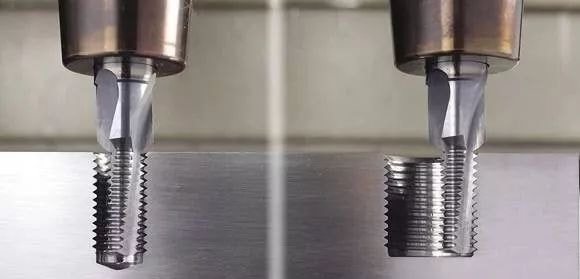
Understanding Thread Machining Principles
Thread machining is a critical process in manufacturing, and understanding its principles is essential for achieving high-quality threads. This process involves cutting or forming threads on a workpiece using a threading tool. Precise control over the cutting speed, cutting edge, and thickness is required to produce accurate threads.
The threading tool is a crucial component in thread machining. Its design and geometry significantly influence the quality of the threads. A sharp and well-maintained cutting edge ensures efficient cutting and minimizes tool wear, which is vital for maintaining thread integrity.
Equally important is the machine tool system, particularly the CNC lathe, renowned for its high precision and flexibility in thread machining. The machine tool host must be appropriately programmed to ensure accurate thread cutting. Additionally, the spindle rotates precisely to maintain the desired thread pitch, ensuring consistency and accuracy in the threads produced.
Understanding these principles helps correctly set up the machine and tools, leading to better performance and higher-quality threads.
Threading Tool Binding
1. Main Causes
(1) The front angle of the cutting tool is too large, and there is significant backlash in the machine’s X-axis screw.
(2) The cutting tool or thread cutter is installed too high or too low, leading to inaccuracies in thread machining.
(3) The workpiece is not securely clamped.
(4) The cutting tool is excessively worn.
(5) The cutting parameters are too large.
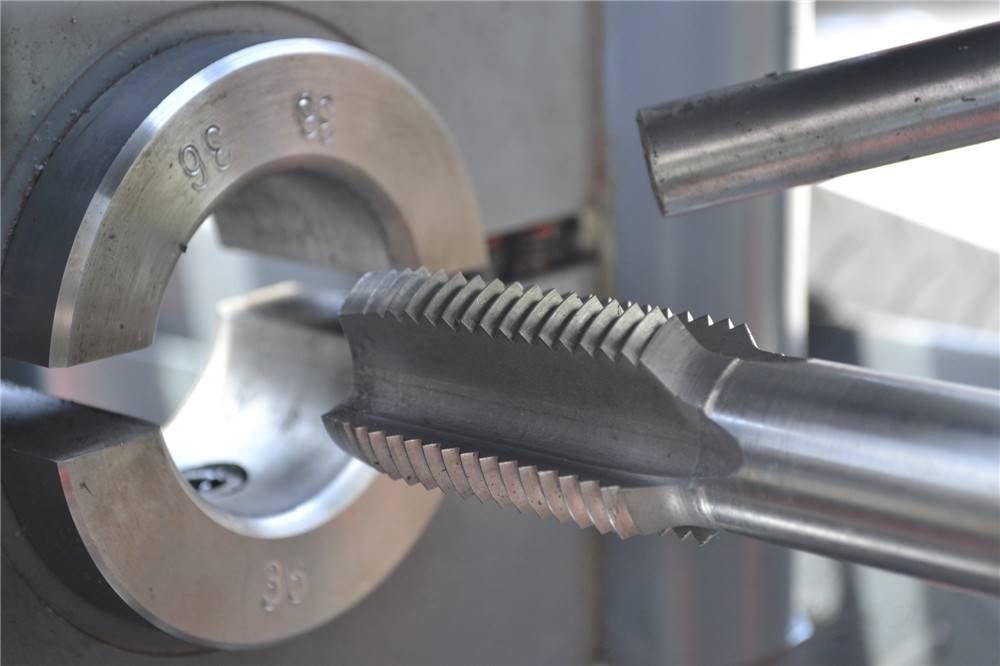
2. Solutions
– (1) Reduce the tool’s front angle, repair the machine, adjust the backlash of the X-axis screw, and use the automatic compensation function of the CNC lathe.
– (2) If the tool is too high, it may cause increased friction and even bend the workpiece, leading to binding. If too low, chips may not be ejected quickly, resulting in increased depth of cut. Adjust the tool height to ensure the tip is level with the workpiece axis (you can use a tailstock center for alignment). During rough and semi-finish turning, the tooltip should be about 1% higher than the workpiece center (D represents the diameter of the workpiece).
– (3) If the workpiece is not securely clamped, it may deflect under cutting forces, causing an increase in cutting depth. Securely attach the workpiece using a tailstock center to enhance rigidity.
– (4) Excessive wear on the cutting tool increases cutting forces and can cause binding. Resharpen the tool as needed.
– (5) Select appropriate cutting parameters based on the workpiece lead and rigidity.
Thread Misalignment
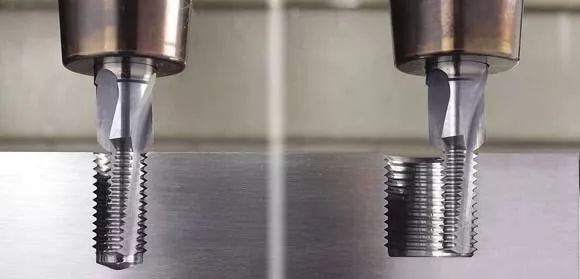
Thread misalignment can occur due to various factors, including incorrect sharpening or alignment of the tooltip. This can lead to significant machining errors, such as thread tooth angle errors and surface roughness issues.
1. Fault Phenomenon
– Misalignment occurs when the screw turns without the workpiece completing an integer turn.
2. Main Causes
(1) The wear of the spindle encoder synchronous belt leads to incorrect detection of spindle synchronous speed.
– (2) Incorrect programming input.
– (3) Worn X-axis or Y-axis screws.
3. Solutions
– (1) If the synchronous belt is worn, repair the machine and replace the spindle synchronous belt.
– (2) To prevent misalignment, ensure that the cutting trajectory of the subsequent pass overlaps with the previous one. In CNC lathes, program the tool to retract after cutting to align the starting position of the next pass with the previous one.
– (3) If there is significant wear on the X-axis or Y-axis screws, repair or replace them.
Incorrect Pitch
Incorrect pitch can often be attributed to issues with the turning tool, such as improper installation, sharpening, or maintenance. Ensuring the turning tool is correctly set up is crucial for achieving high precision and avoiding problems like thread accuracy, tool wear, and surface roughness of the finished product.
Main Causes of Incorrect Pitch
– Inaccurate data transmitted from the spindle encoder to the machine system; excessive play in the X-axis or Y-axis screws; incorrect programming input.
2. Solutions
(1) If data transmission is inaccurate, Repair the machine or replace the spindle encoder or synchronous belt.
– (2) Adjust the spindle axial play and use the system’s automatic compensation for X-axis or Y-axis play.
– (3) Verify the program to ensure that the lead in the instructions matches the design requirements.
Incorrect Tooth Profile
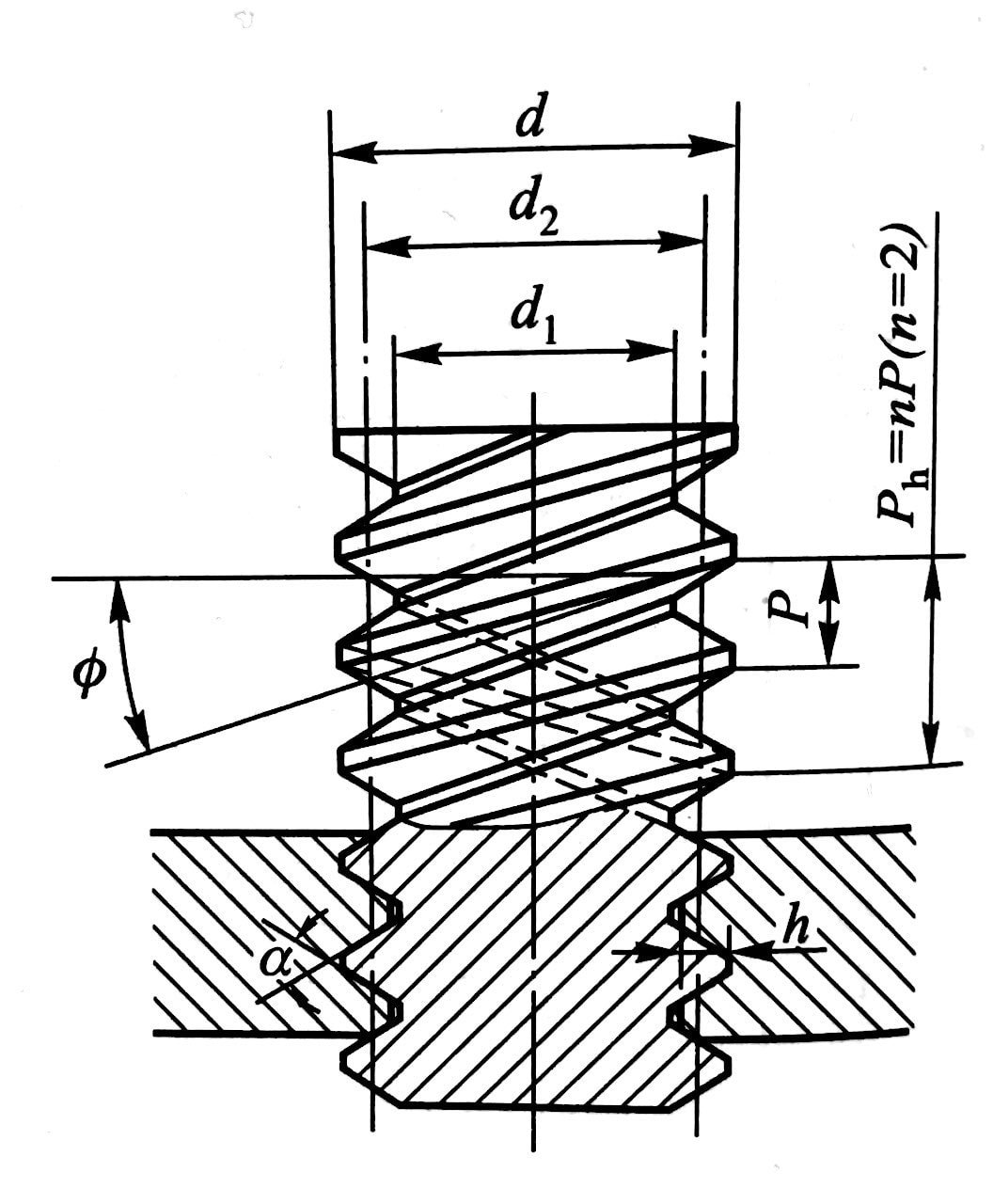
Leading Causes of Incorrect Tooth Profile
Incorrect sharpening of the turning tool tip; improper installation of the turning tool tip; tool wear.
2. Solutions
– (1) Correctly sharpen and measure the cutting tool angle. For threads with high precision requirements, use a standard mechanical fixture for threading or sharpen the thread tool on a grinding machine.
– (2) Use a template for tool setup or align the threading tool using a dial indicator.
– (3) Select appropriate cutting parameters based on machining conditions and resharpen the tool promptly.
High Surface Roughness of Threads
1. Main Causes
(1) Buildup on the tooltip.
(2) Insufficient rigidity of the tool holder, leading to vibrations during cutting.
(3) Excessive radial front angle of the tool.
(4) Turning tool wear can increase cutting forces and lead to improper chip ejection during high-speed cutting.
(5) Poor rigidity of the workpiece with excessive cutting parameters.
(6) Rough surface of the cutting tool.
Solutions for High Surface Roughness of Threads
– (1) When using high-speed steel tools, reduce the cutting speed and select the appropriate cutting fluid.
– (2) Increase the toholder’sr’s cross-section and reduce its extended length.
– (3) Reduce the radial front angle of the tool.
– (4) Ensure that the chip thickness during the last cut exceeds 0.1 mm and that chips are ejected along the vertical axis.
– (5) Choose appropriate cutting parameters.
– (6) The roughness of the cutting edge should be 2-3 grades lower than that of the machined surface.
In summary, the faults encountered during thread turning can be diverse, stemming from equipment, tools, or operator issues. It is essential to analyze each situation, using various detection and diagnostic methods to identify influencing factors and apply practical solutions.
Optimizing Thread Machining Performance
Optimizing thread machining performance requires carefully balancing several factors, including cutting speed, cutting edge, and cutting thickness. The cutting speed must be optimized to ensure efficient cutting and minimize tool wear. While a higher cutting speed can lead to faster production times, it may also increase tool wear and reduce thread quality if not managed properly.
The cutting edge of the threading tool must be sharp and well-maintained. A dull cutting edge can result in poor thread quality and increased tool wear, compromising the machining process. Regular maintenance of the threading tool is essential to ensure it remains in optimal condition.
Cutting thickness also plays a critical role in thread machining. It must be optimized to ensure accurate threads and minimize tool wear. While a thicker cutting thickness can speed up production, it may also lead to increased tool wear and reduced thread quality if not carefully controlled.
By paying attention to these factors, manufacturers can enhance thread machining performance, resulting in higher-quality threads and more efficient production processes.
Best Practices for Thread Machining
Adhering to best practices in thread machining involves careful consideration of several factors, including tool selection, cutting speed, and the use of cutting fluid. The threading tool must be chosen based on the specific thread machining application, ensuring it is suitable for the material and thread type.
Cutting speed must be optimized to ensure efficient cutting and minimize tool wear. This involves finding a balance that allows for fast production without compromising tthreads’ds’ quality or ttool’sl’s longevity.
The use of cutting fluid is also crucial. It must be selected based on the specific thread machining application and applied at the correct pressure and flow rate. Cutting fluid helps to cool the cutting edge, reduce tool wear, and improve thread quality by facilitating smoother cutting and chip removal.
Regular maintenance of the threading tool is essential for optimal performance. This includes inspecting the tool for wear and damage and replacing or repairing it as needed. The machine tool system must also be adequately maintained for accurate thread cutting and overall performance.
By following these best practices, manufacturers can optimize thread machining performance, improve thread quality, and reduce production costs, leading to more efficient and reliable manufacturing processes.