In project development, estimating the machine tool life as a reference for budgeting and planning is often necessary. Failing to manage tool life properly can lead to catastrophic tool failure, significantly impacting production efficiency and costs. Understanding the factors affecting tool life, such as workpiece hardness, cutting rates, tool materials like cemented carbide tools, and appropriate cutting conditions, is crucial for accurate estimation. Usually, it is necessary to investigate and understand the consumption of cutting tools in similar processing forms for the same industry and products. Based on this, a maturity and accuracy assessment should be conducted to determine the predetermined value of the corresponding tool life for the enterprise. Additionally, capturing accurate machine tool data is essential for predicting tool failures, improving maintenance schedules, and enhancing overall machining efficiency. However, they often hope to obtain tool life data in a more direct form for various reasons.
Understanding Tool Life
Tool life is a critical aspect of machining that directly impacts production efficiency, costs, and the quality of the finished product. In essence, tool life refers to the duration a cutting tool can effectively perform its intended function before it needs to be replaced due to wear or failure. Accurately estimating tool life is essential for planning maintenance schedules, budgeting tool replacements, and ensuring consistent production quality.
Several factors influence tool life, including the material of the workpiece, cutting speed, feed rate, depth of cut, and the cutting tool used. By understanding these factors and their interactions, manufacturers can optimize their machining processes to extend tool life, reduce costs, and improve overall productivity.
Taylor’s formula
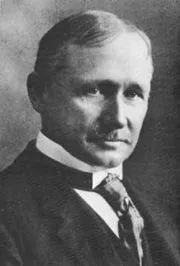
In the theoretical discipline of mechanical processing, Taylor’s tool life equation is commonly used to represent the relationship between tool durability (T) and linear velocity (V). Taylor’s tool life equation calculates and predicts the lifespan of cutting tools in machining processes. VTm=C1, known as the T-V relationship, has different coefficients and indices depending on the workpiece material, tool material, and cutting conditions. You can draw different tool durability relationship charts in the double curve coordinate system, called T-V charts. Similarly, equations and charts show the relationship between T and f (feed rate) and ap (cutting depth).
The Taylor formula is used in classrooms and laboratories and is rarely used in factories. Factories are accustomed to using estimation methods to obtain tool durability or tool service life. There are generally several estimation methods as follows:
1. According to cutting time:
In the metal-cutting tool industry, the recommended cutting line speed is based on a tool life of 15 minutes. In practical use, the recommended value of the tool brand manufacturer is generally taken as 75%, and the tool life is about 60 minutes.
Tool life curves can be plotted to analyze how different factors, such as cutting speed and feed rate, influence the lifespan of cutting tools.
The number of workpieces that can be machined by one blade can be estimated according to the following formula:
N=(19100XVXf)/(DXh)
N – Tool life, number of workpieces that can be machined, unit: piece
V – Tool selection cutting line speed, unit: meter/minute
F – Feed rate during processing, unit: millimeters per revolution
D – Diameter of the workpiece being processed, unit: millimeters
H – Processing length, millimeters
Example: Turning a workpiece with a diameter of 50 millimeters and a length of 100 millimeters, the tool manufacturer recommends a line speed of 200 meters per minute, the predetermined cutting time and lifespan of the tool are T=60 minutes, and the actual used line speed is 150 meters per minute, with a feed rate of 0.1 millimeters per revolution. Estimated tool lifespan:
N=(19100X150X0.1)/(50X100)=57.3
According to the above conditions, each blade can process 57 workpieces.
2. Measured by cutting distance:
The cutting distance refers to the distance traveled by a blade from the beginning to failure, assuming it continuously cuts at a certain speed on a very large workpiece. This distance is called the cutting distance life and is represented by L.
In CNC machining, practical tool wear and failure management are crucial for maximizing efficiency and reducing scrap parts.
The number of workpieces that can be machined by one blade can be estimated according to the following formula:
N=(318300XLXf)/(DXh)
N – Tool life, number of workpieces that can be machined, unit: piece
L – Estimated lifespan of cutting distance, unit: kilometers
F – Feed rate during processing, unit: millimeters per revolution
D – Diameter of the processed workpiece, unit: millimeters
H – Processing length, millimeters
Example: Turning a workpiece with a diameter of 50 millimeters, a length of 100 millimeters, a feed rate of 0.1 millimeters per revolution, and a cutting distance of 10 kilometers, as introduced by the tool manufacturer. Estimated tool life:
N=(318300X10X0.1)/(50X100)=63.66
According to the above conditions, each blade can process 63 workpieces.
3. Based on experience points:
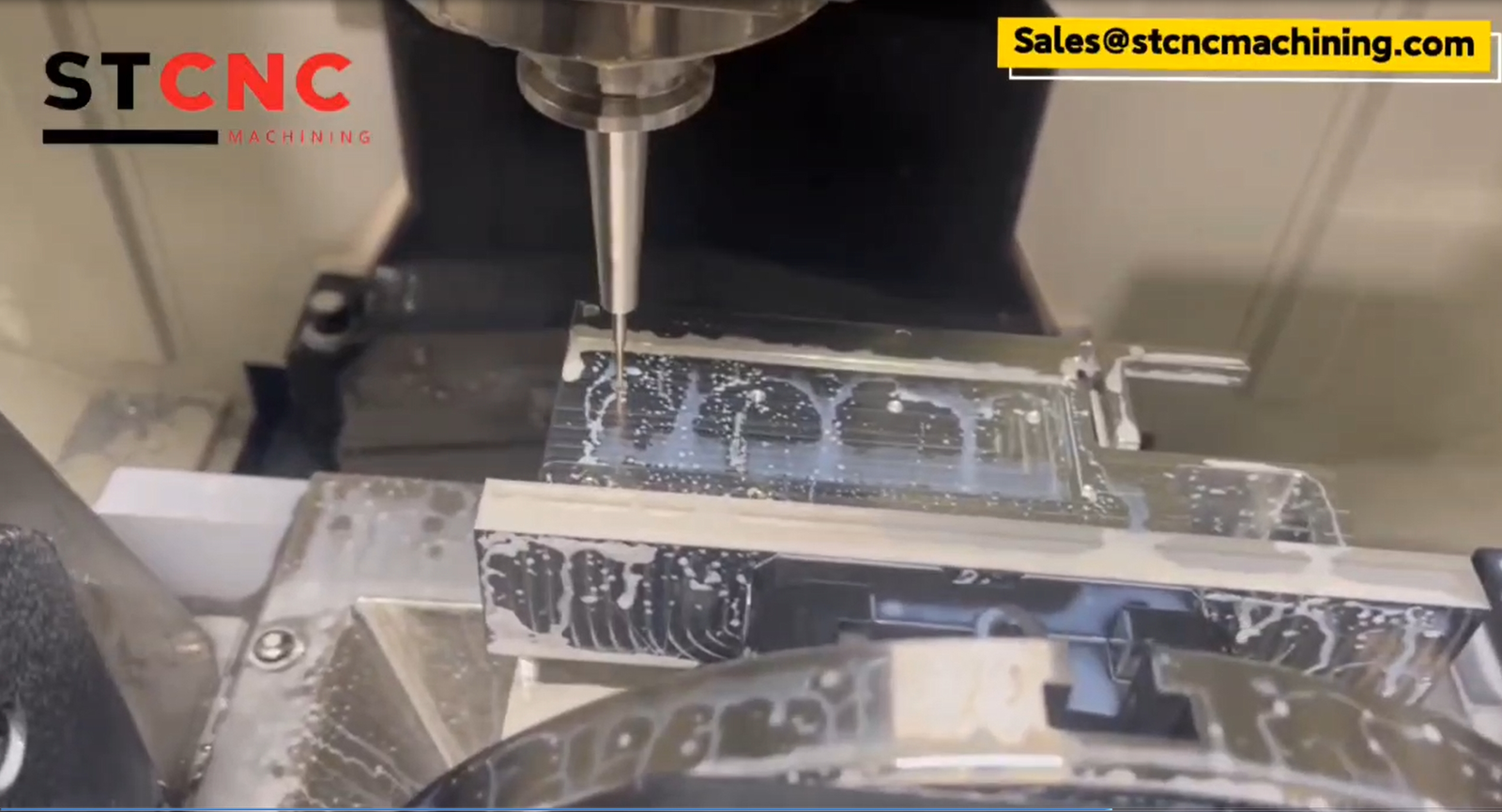
Experienced practitioners have accumulated rich experience estimating the service life of commonly used materials and tools when processing a specific type of material workpiece. They can directly estimate the service life of tools.
For coated tricky alloy drill bits with diameters between 25 and 30, the drilling length for processing ordinary carbon steel is approximately 20 to 30 meters, with a cumulative length. When processing cast iron, the cumulative total length is generally between 80 and 100 meters.
The three estimation methods mentioned above are only approximate estimates under normal circumstances. Whether calculated based on cutting time or cutting distance, they are both relatively conservative. Because few tool manufacturers provide this data, even if provided, it is only a particular case of the provider under specific environmental conditions in the laboratory and may not have universal guiding significance.
However, estimating based on empirical values has significant limitations. It may not necessarily have universal commonalities and can only be roughly estimated under similar conditions. However, this estimation method is closer to reality for a particular brand and a specific type of tool in processing certain materials. Under the same or similar conditions, it can be used as a reference.
Tool life curves can be plotted to analyze how different factors, such as cutting speed and feed rate, influence the lifespan of cutting tools.
When estimating in practice, the following conditions must also be considered:
Factors Affecting Tool Life
Understanding the factors affecting tool life is crucial for optimizing machining processes. These factors can be broadly categorized into the following:
1. To Determine the Failure Limit
Determining the failure limit of a tool is crucial in understanding tool life. The failure limit is when a tool can no longer perform its intended function, resulting in reduced productivity, increased costs, and potential damage to the machine or workpiece. Factors such as cutting speed, feed rate, and depth of cut can all impact the failure limit of a tool. For instance, in precision machining, a tool may be considered to have failed if it causes a deviation in the workpiece’s dimensions or surface finish. By identifying the failure limit, manufacturers can set appropriate tool replacement schedules to avoid catastrophic tool failure and maintain consistent production quality.
2. The Cutting Speed’s Impact
Cutting speed is a critical factor affecting tool life. As cutting speed increases, tool life decreases. This is because higher cutting speeds generate more heat, which can lead to tool wear and failure. However, cutting speed also affects the material removal rate, so finding the optimal balance between cutting speed and tool life is essential. For example, while a higher cutting speed can increase production rates, it may also reduce the tool’s lifespan, leading to more frequent replacements and higher costs. Therefore, manufacturers must carefully select cutting speeds based on the specific machining conditions and tool materials to maximize efficiency and tool life.
3. Material of the Workpiece
The material of the workpiece also plays a significant role in determining tool life. Different materials have varying hardness, toughness, and thermal conductivity levels, which can affect the cutting process and tool wear. For example, cutting tools used on hard materials like steel or titanium may have a shorter tool life compared to those used on softer materials like aluminum or copper. Also, the workpiece material’s abrasive particles or inclusions can accelerate tool wear. Manufacturers can optimize tool life and machining performance by selecting appropriate tool materials and cutting conditions for different workpiece materials.
In addition to these factors, other considerations such as tool material, cutting-edge geometry, and machine tool data can also impact tool life. By understanding these factors and their interactions, manufacturers can optimize their machining processes to extend tool life, reduce costs, and improve overall productivity.
It’s worth noting that Taylor’s t equation is a widely used formula to predict tool life based on cutting speed and other factoThe equation is VT^n = C, where V is the cutting speed, T is the tool life, n is Taylor’s tool life exponent, and C is a constant. By understanding the factors that affect tool life and using tools like Taylor’s equation, manufacturers can make informed decisions to optimize their processes and improve their bottom line.
Furthermore, machine tool data and analytics can also help manufacturers better understand tool life and optimize their machining processes. By collecting and analyzing data on tool performance, manufacturers can identify trends and patterns that can inform their decision-making and improve their overall efficiency.
In conclusion, understanding tool life is critical for manufacturers to optimize the machining processes and improve productivity. By considering factors such as cutting speed, workpiece material, and tool material, manufacturers can extend tool life, reduce costs, and improve overall efficiency. Tools like Taylor’s equation and machine tool data analytics can also help manufacturers make informed decisions and optimize their machining processes.
1. To determine the failure limit, that is, under what circumstances the tool cannot be used.
Except for extreme conditions such as blade breakage and rupture. Mainly referring to wear, especially during precision machining, it is generally considered normal for the blade surface to wear within 0.2 millimeters after precision machining. Titanium Hao Machinery is the company’s primary product, including rotary top, screw, machine tool spindle, shaft machining, high-precision tool holder, tool holder, elastic chuck, non-standard part machining, and machine tool connecting rod! But if it is a fixed-diameter tool, the wear of the back-cutting surface will cause a change in the diameter of the workpiece. The tool must be replaced once there is a dangerous radial size change. For example, if there are special requirements for surface roughness, and the tool is slightly worn, or the surface roughness decreases somewhat, which cannot meet the criteria, the tool must also be replaced. When estimating, it is necessary to lower the estimated value according to a certain proportion. If adjustments or compensations exist in the radial dimension and the surface roughness requirements are relatively low during processing, the estimated value can be increased proportionally.
2. The cutting speed significantly impacts the wear of cutting tools.
Generally speaking, the faster the linear speed, the shorter the tool life. However, if the linear speed is too low, it will not only affect the machining efficiency but may also not necessarily benefit the tool life. Therefore, the cutting speed selection must refer to the cutting parameters provided by the tool manufacturer, and the most reasonable speed must be determined based on the on-site situation.
3. The material of the workpiece being processed also significantly impacts the tool life.
Seemingly identical materials with slightly different proportions of internal material composition may result in significant differences in cutting performance. Significant differences in tool life can occur even with similar materials, such as different component structures, molding methods, heat treatment equipment or processes, and cutting tools for previous processes. Titanium Hao Machinery is the company’s main product, including rotary top, screw, machine tool spindle, shaft machining, high-precision tool holder, tool holder, elastic chuck, non-standard part machining, and machine tool connecting rod! For the processing of stainless steel parts, if the tool used for rough machining in the previous process is not sharp, a hardening layer is formed on the surface of the workpiece due to the cold work hardening effect, resulting in rapid wear of the precision machining tool in the subsequent process, which seriously affects the service life of the precision machining tool.
4. Reasonable and accurate use of cutting fluid can significantly improve tool life.
Firstly, the cutting fluid must be correct, clean, sufficient, and adequate. Different tool materials, workpieces, and machining forms should be filled with varying cutting fluids according to the purpose requirements, such as cooling during rough machining and lubrication during precision machining.
5. The foundation, machine tools, fixtures, workpieces, cutting tools, and everything else form a system, and the rigidity of the entire system significantly impacts the tool’s life.
Due to small vibrations causing abnormal macro displacement between the tool and workpiece, the tool unnecessarily increases ineffective friction, ultimately leading to tool wear and a rapid decline in tool life. Improving system rigidity is an important measure and means to enhance tool life. Still, it is necessary to continuously conduct detailed and complex investigations, analyses, and research work to improve system rigidity effectively. Many people believe that changing the structure of a particular area would incur significant economic costs, but this is not the case. A one-time investment in workforce and material resources may result in a long-term reduction in consumable expenses for several years or even more than a decade.
The above refers to turning and boring situations and can also be used as a reference for machining, such as drilling, expanding, and reaming. Milling processing is significantly different from it:
Milling is intermittent cutting, and the material of the tool edge should be impact resistant, have good toughness, relatively low hardness, and relatively poor wear resistance.
Milling is intermittent machining, and the actual cutting time at the cutting edge is only 30% to 50% of the total machining time, which is beneficial for heat dissipation at the cutting edge and can effectively extend the tool life.
Different machining forms are used during the machining process, such as end-face milling, circumferential milling, surface milling, and groove milling. Other parts, such as the leading and auxiliary cutting edge, and different processing requirements, such as rough milling, precision milling, etc., have significant differences in failure modes. The tool life situation is also different.
The milling cutter is a multi-blade tool, and the above formula cannot be used to calculate it. Generally, borrowing can only be analyzed and approximate estimates made based on actual situations.
Estimating tool life is crucial for managing production efficiency and costs. Various methods, including Taylor’s’ formula, cutting time, cutting distance, and empirical experience, help predict tool wear. Taylor’s’ formula offers a theoretical approach but is less practical in real-world conditions. Cutting time and distance methods provide more direct estimates, though they can be conservative. Based on experience, empirical estimation is the most practical but is limited to specific conditions.
Key factors affecting tool life include cutting speed, workpiece material, tool material, cutting fluid, and system rigidity. By considering these factors and using a combination of estimation methods, manufacturers can improve tool life predictions, optimize tool usage, and enhance overall machining efficiency.
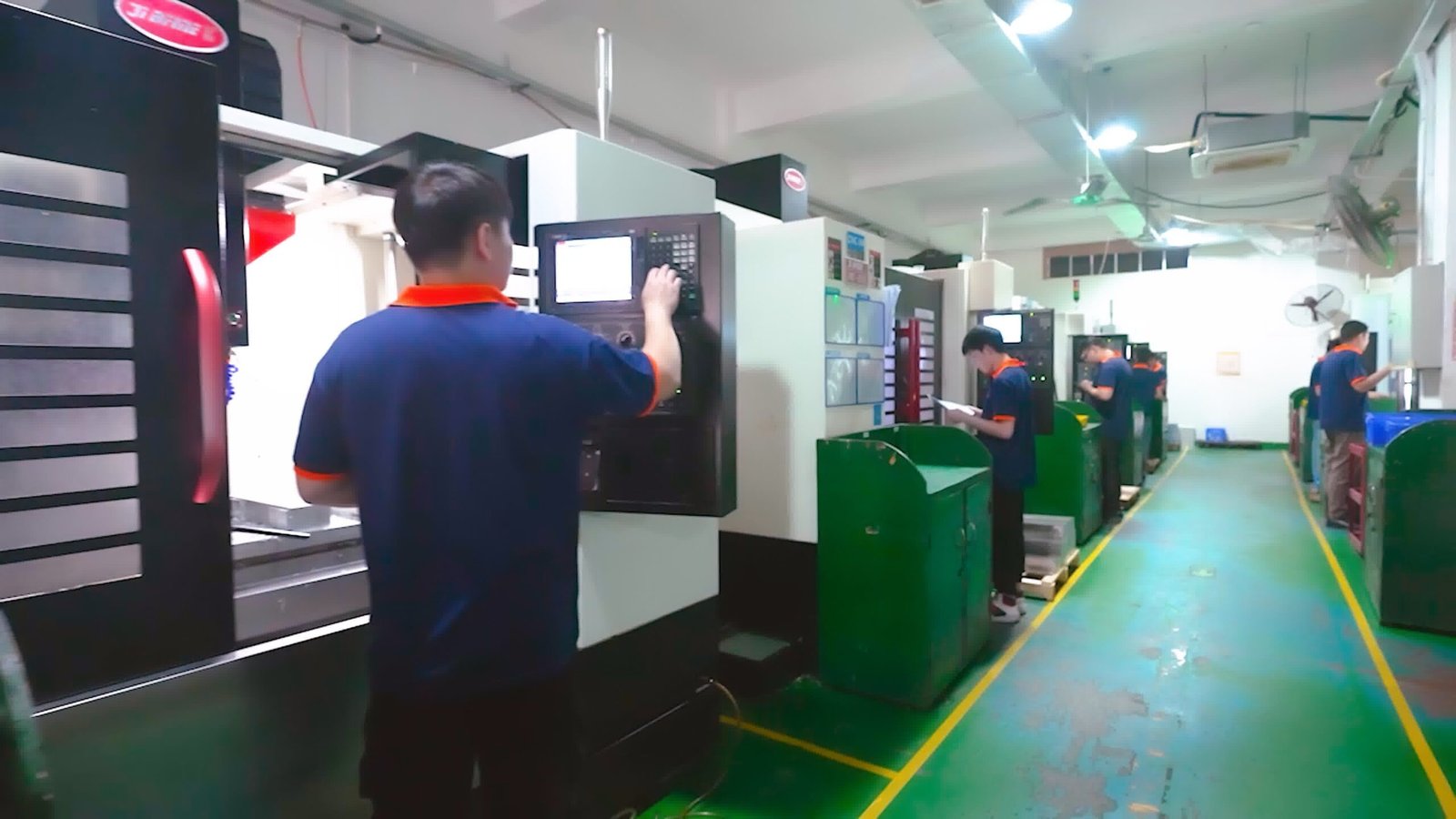