What is milling machine?
Milling machine is a machine tool used to machine solid materials, such as metal, wood,or plastics. The machine consists of a cutting tool that rotates and moves along multiple axes to remove material from the workpiece in order to shape it into the desired form.
Milling machines are used in a wide range of industries, including manufacturing, aerospace, automotive, and construction. They are commonly used for tasks such as drilling, cutting, and shaping materials, and are capable of producing a wide range of complex geometries and designs.

What is CNC Milling?
CNC milling, short for Computer Numerical Control milling, is a manufacturing process in which a computer-controlled machine removes material from a workpiece to create a desired shape.
The process begins with a 3D design or model of the object, which is then translated into instructions sent to the milling machine. The machine is equipped with a cutting tool that can move in multiple directions along several axes, guided by the instructions from the computer program.
During the CNC milling process, the cutting tool removes material from the workpiece until the desired shape is achieved. This can be done using various cutting tools, including end mills, drills, and other specialized tools, depending on the shape and complexity of the milling object.
CNC milling is an exact and versatile process used in various industries, including aerospace, automotive, and medical device manufacturing. It can create everything from flat shapes to highly complex 3D objects with intricate details and precise tolerances.
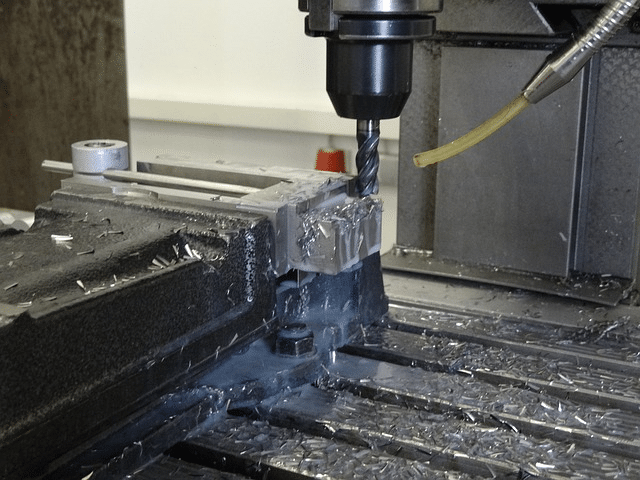
What parts are suitable for production on a CNC machine?
We specialize in CNC machining engineering plastics: PEEK, PVC, PTFE, PP, PI, Nylon, aluminum alloy, stainless steel, carbon steel, cobalt-chrome, copper, and various ceramics including silicon carbide.





Characteristics of CNC milling machine and the details that can be processed
Characteristics
1. Flexible and multi-purpose
CNC milling machines and machining centers are suitable for processing workpieces of various structures and shapes and can complete drilling, boring, reaming, milling, milling, groove milling, milling (cam), tapping, etc.
2. High processing precision
CNC milling machines and machining centers have high machining accuracy and can guarantee the accuracy of workpieces under normal circumstances. CNC machining also avoids operator errors, and the size uniformity of parts processed in the same batch is excellent, significantly improving product quality.
3. High production efficiency
The machining center has a milling machine, a boring machine, and a drilling machine. The function makes the process highly concentrated, significantly improving production efficiency and reducing the workpiece clamping error. The machine’s spindle speed offers a continuously variable transmission to help you choose the best cutting amount. CNC milling machines are fast-forwarding. Fast winding and fast forward function can significantly reduce maneuvering time.
4. Complicated shapes can be processed
Ordinary milling machines can not only mill the surfaces of various parts that can be milled by ordinary milling machines but also mill plane curve profiles and space surface profiles that ordinary milling machines cannot mill. This is because the CNC machine tool has multiple feed coordinates. Axial linkage function.
5. Reduce the labor intensity of the operator
The CNC milling machine automatically completes the part processing according to the pre-programmed processing steps. In addition to operating the keyboard, the operator uses the keyboard. They were loading and unloading tools and measuring workpieces and intermediate parts. In addition to observing the movement of the machine tool, there is no need for heavy movements. Repeated manual operations greatly reduce labor intensity.
Parts that the CNC milling process
1. Processing parts with complex shapes
Compared with ordinary machines, CNC milling machines have high processing precision, complex shapes of processed parts, and a wide processing range. According to the characteristics of the CNC milling machines, the content suitable for CNC milling machine processing mainly includes the following categories: complex structures such as curved contours or curved surfaces. The planar, curved profile of the workpiece. This means parts with complex curved inner and outer shapes, with treated surfaces parallel or perpendicular to horizontal planes. In the CNC milling process, we usually only need to use the two-coordinate linkage of the three-coordinate CNC milling machine to process them.
2. Workpiece structures that are difficult to process with ordinary milling machines
For dimensions, markings, and ordinary milling machines suitable for CNC milling machines, CNC milling machines should be selected.
3. Ordinary milling machines cannot achieve precision and accuracy
When processing with an ordinary milling machine, it is difficult to guarantee the dimensional accuracy, shape/position accuracy, and surface roughness of the workpiece, so choosing a CNC milling machine for processing is necessary.
4. Parts with reasonable consistency requirements:
In large-scale production, the CNC milling machine has high positioning and repeat positioning accuracy, which can avoid errors caused by human factors in the process of ordinary milling machines. The CNC milling machine can easily guarantee success. The consistency of batch parts improves the machining accuracy and makes the quality more stable.
How is CNC Milling Done?
To carry out CNC milling on any workpiece, it is first necessary to connect the workpiece to the machine. At this stage, it is performed to define the reference points of the part to the machine. The reference points of the part to the machine are defined by a precision receiving tip called a probe. The task of the probe tip is to transmit the raw size of the workpiece and its position on the machine to the machine. During milling, cutting tools thus have the opportunity to work with zero defects. After the part settles on the workbench, the cutting tools are placed in a special mechanism. The name of this mechanism is the magazine. CNC milling continues with the introduction of other mechanical systems that ensure the movement of the workpiece.
What are the Operations Performed on CNC Milling Machine?
If you have an excellent CNC milling machine in your business, it is possible to carry out many of your manufacturing processes with it successfully. One of the most curious questions about CNC milling is, “What does a CNC milling machine do?” To put it briefly, milling machines, first of all, work on flat and angled surfaces. This process takes place in the form of chip removal from the surface and is also known as face milling. In addition, channel and threading and flat and circular partition-making are among the processes on milling machines. These machines’ main parts, heads, and other accessories make it easy to carry out CNC milling for various purposes. The names of the operations in the machines come from two primary sources.
What is CNC Face Milling?
One of the most common milling jobs in face milling. During this process, the milling machine needs different tools. CNC programs harmoniously run the tools. The most important feature of these programs is that they give a flexible structure to CNC machine management works. This makes it easier to make changes to programs or undo changes. In face milling, milling cutters with 45-degree input angles are more in the foreground. However, within the framework of operator programming, round-end or edge mills also work in a coordinated manner during face milling. In this way, CNC milling angle machining on the surface takes place flawlessly.
What is CNC Milling Threading?
Threading is opening a thread slot into a hole in the workpiece. In this process, milling boring operations take place without using a guide. The computer controls special milling knives in CNC milling. The threading process of the cutting tools thus takes place with zero errors. In industrial manufacturing, CNC milling threading usually occurs with pool machining, side top-up machining, and channel opening. In addition, procedures such as hole augmentation accompany these processes. CNC milling technology finishes very long jobs quickly with human power.
What are the Advantages of a CNC Milling Machine?
CNC Machining Advantages
The advantages of CNC machines compared to conventional machining methods are numerous; these machines use higher levels of automation and reduce possible errors while increasing productivity and cost-effectiveness across the board. Here is a compilation of the main advantages of CNC machines:
Productivity
Because you can program a CNC mill or other machine to perform a complex series of actions, you can often step away while the machine gets to work. This can include out-of-hours automated machining in specific set-ups, hugely increasing your productivity and rate of output. This is particularly true for precision engineers operating several CNC centers, such as Oracle Precision.
Consistency
Because using a CNC almost eliminates human error, CNC machines are highly consistent and accurate in their work, providing clients with uniform and faultless products. This makes CNC machining so crucial for areas where quality is critical, as the level of reliability and quality in work produced is much higher.
Cost-Effectiveness
CNC machines more than makeup for their initial costs with a high output rate and fewer mistakes in resulting components. Operators also require less training to operate a CNC machine and can learn how to use the machine in a virtual environment, eliminating the need for training workpieces. As these machines become more popular and widespread, their cost will continue to drop.
Safety
Any hazardous safety issues, such as a jam or other machining error, are only detrimental to the machine and not a safety issue for the operator, unlike conventional open guard machining.
Versatility
CNC machines can be reprogrammed quickly to produce a completely new product, making them ideal for short or long production runs. You can change programming without it being time-consuming or too costly.
What are the main differences between CNC milling machines and common milling machines?
Different in nature
1. CNC milling machine: It is an automatic processing equipment developed based on general milling machines. The processing technology of the two is basically the same, and the structure is somewhat similar. CNC milling machines are divided into two categories without tool magazines and with tool magazines. The CNC milling machine with tool magazine is also called a machining center.
2. Common milling machine: The typical milling machine is a machine tool usually used for various surface processing of the workpiece. It uses a rotating milling cutter to clamp the workpiece on the workbench and move the cutter to cut the workpiece, thus forming the required shape and profile. Common milling machines are usually suitable for processing metal and non-metallic materials, such as steel, aluminum alloy, copper, plastic, etc. In the machining and manufacturing industry, the common milling machine is a common machine tool often used to manufacture various mechanical parts, molds, tools, and other complex parts.
Application characteristics
1.CNC milling machine: With the rapid development of social production and science and technology, mechanical products are becoming more and more sophisticated and frequently modified, especially for mechanical parts required in aerospace, shipbuilding, military and other fields, which require high precision and complex shapes, small batches. Processing such products requires frequent modification or equipment adjustment, and ordinary machine tools or highly specialized automatic machine tools can no longer meet these requirements.
2. Common milling machine: It has strong adaptability and good flexibility in parts processing and can process parts with particularly complex contour shapes or difficult-to-control sizes, such as mold parts, shell parts, etc.; can process standard machine tools that cannot be processed or are challenging to process Parts, such as complex curve parts and three-dimensional space surface parts described by mathematical models.
Extended information:
In addition to the characteristics of standard milling machine processing, CNC milling processing has the following features:
1. Parts processing has strong adaptability and flexibility and can process parts with particularly complex contours and shapes or difficult-to-control sizes, such as mold parts, shell parts, etc.;
2. It can process parts that cannot be processed by ordinary machine tools or are challenging to process, such as complex curve parts described by mathematical models and three-dimensional space surface parts;
3. It can process parts that need to be processed in multiple processes after one clamping and positioning;
4. High processing precision and stable and reliable processing quality. The pulse equivalent of the numerical control device is generally 0.001mm, and the high-precision numerical control system can reach 0.1μm. In addition, the numerical control processing also avoids the operator’s operating errors;
What are the three basic types of milling machines?
1.Vertical milling machine.

2.Horizontal milling machine.

3.Universal milling machine.
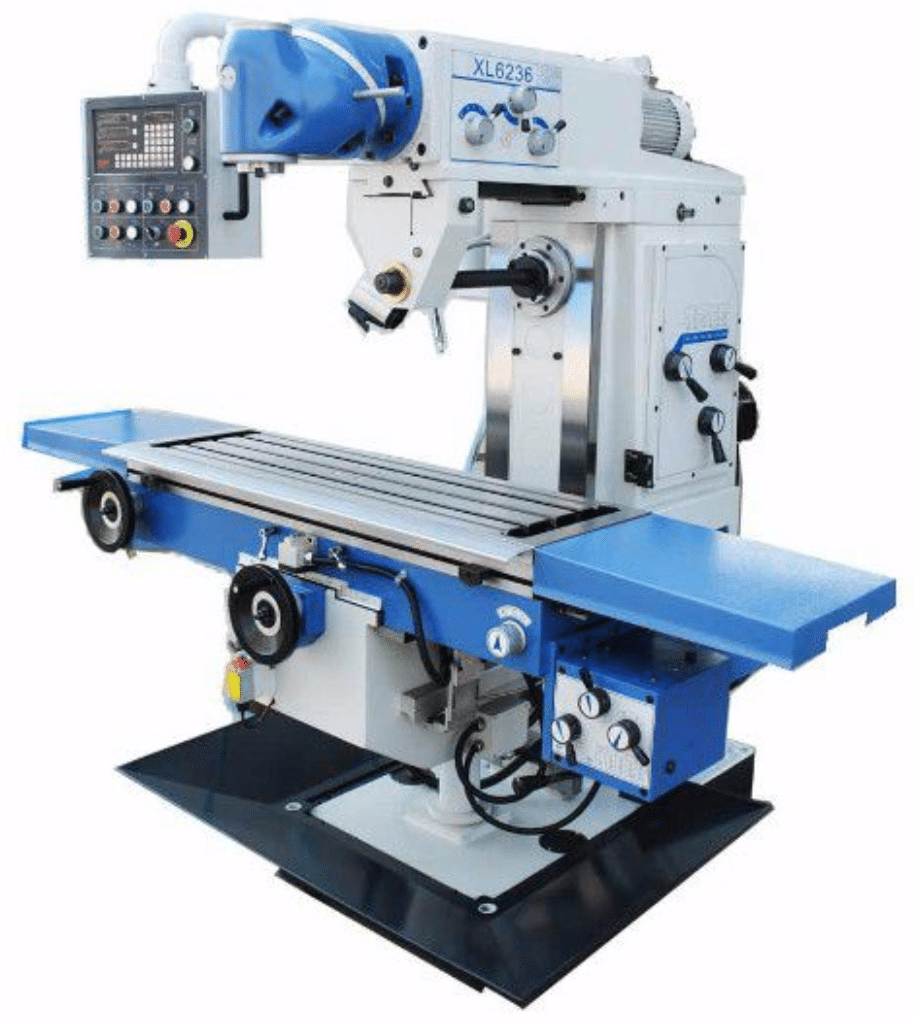
What is a vertical milling machine?
A vertical milling machine is a machining tool that uses a vertically oriented spindle to rotate a cutting tool against a workpiece, typically to remove material and shape the workpiece into the desired form. Vertical milling machines are commonly used in manufacturing and metalworking applications to create parts and components with high precision and accuracy. They can perform various operations, including drilling, cutting, and shaping, and are often used with computer numerical control (CNC) technology for greater automation and efficiency.
What is a horizontal milling machine?
A horizontal milling machine is a type of milling machine that has a horizontally oriented cutting tool, with the workpiece being fed in from the side. It removes material from a workpiece by rotating a cutter with multiple teeth, which is then moved horizontally across the surface of the workpiece. Horizontal milling machines are often used for large-scale production and can create complex shapes and features in metal, plastic, and other materials.
What is a universal milling machine?
A universal milling machine is a type of milling machine that has a swiveling table and can perform horizontal and vertical milling operations. This machine can cut and shape various types of materials, including metal, wood, and plastic, and is commonly used in industrial and manufacturing settings. The swiveling table allows the operator to angle the workpiece in different directions, making it possible to create complex shapes and contours. Universal milling machines are also equipped with various cutting tools, making them versatile and suitable for various machining applications.
The structural composition of the milling machine and the functions of each part:
The CNC milling machine has multiple functions a milling machine, a boring machine, and a drilling machine, so its process is highly concentrated. Only the processing program, clamping tool, and adjustment tool data are stored in the CNC device when the workpiece is replaced. The production cycle is greatly shortened, and production efficiency is improved.
A typical CNC milling machine is divided into six parts. Here is a brief introduction to the structure and the function of the CNC milling machine:
1. Machine body
The internal reinforcement ribs of the machine body are reasonably arranged and have good rigidity. There are four adjusting bolts on the base to facilitate the level adjustment of the machine tool. The cutting oil pool is placed inside the bed.
2. Milling head part
The milling head part comprises two parts: a stepped gearbox and a milling head. The milling head spindle is supported on high-precision bearings to ensure that the spindle has high rotation accuracy and good rigidity. The main shaft is equipped with fast-acting cluster cutter nuts and adopts mechanical step-less speed change, a wide adjustment range, stable transmission, and convenient operation. The braking mechanism can quickly brake the main shaft, saving additional time. When braking, it needs to use the brake handle to open the stop ring to make the spindle brake immediately. We should focus on loosening the spindle brake handle when starting the main motor. The milling head component is also equipped with a servo motor, an internally toothed belt wheel, a ball screw pair, and a spindle sleeve, which forms a vertical feed transmission chain to make the spindle move linearly in the vertical direction.
3. Workbench
The working table and the bed saddle are supported on the wide horizontal guide rail of the lifting table. The longitudinal feed of the worktable is driven by a servo motor installed at the right end of the worktable. The precision ball screw pair is driven by the internally toothed belt wheel so that the worktable can obtain longitudinal feed. The left end of the worktable is equipped with a hand wheel and a dial for manual operation of the feed, which improves the wear resistance of the guide rail, the smoothness of movement, and the retention of precision and eliminates the phenomenon of low-speed crawling.
4. Horizontal infeed part
An AC servo motor is installed before the lifting platform to drive the saddle for lateral feed movement. Its working principle is the same as the longitudinal feed of the worktable. In addition, a feed handwheel is installed at the front end of the horizontal ball screw to realize manual feed.
5. Lifting platform
There is a locking handle on its left side, and a long handle on its front end can drive the bevel gear and the lifting table screw to rotate, thereby obtaining the lifting movement of the lifting table.
6. Cutting oil cooling system
The cooling comprises a cutting oil pump, oil outlet pipe, oil return pipe, switch, and nozzle. The cutting oil pump is installed in the inner cavity of the base of the machine tool. It pumps the cutting oil from the oil reservoir to the oil outlet pipe and then sprays it through the nozzle to cool the cutting area. The lubrication part adopts the motorized lubrication method to lubricate the spindle sleeve, the guide rail, and the ball screw through the oil separator to improve the service life of the machine tool.
The CNC milling machine has undergone great changes in the overall layout, appearance, transmission system, significant turn of the tool system, and operating mechanism. These changes meet the requirements of CNC milling machines and give full play to the characteristics of CNC milling machines.
In summary, CNC milling is a critical manufacturing technology used in various industries to produce parts and components. Through automation and precise cutting, CNC milling can increase production efficiency while maintaining high-quality parts.
Stcnc Machining offers the proper CNC milling process and machines to meet your Special needs. Contact us and get the DFM feedback right now!
Useful Article ? Share With your friends.