The application and development of lubrication cooling technology in machining continues to revolutionize industrial manufacturing processes. From traditional oils to modern synthetic and eco-friendly coolants, the importance of these technologies lies in their ability to enhance precision, reduce waste, and mitigate environmental impact. Our comprehensive exploration outlines the progression of lubrication cooling solutions and their implications for the future of machining.
Key Takeaways
Lubrication cooling technology in machining has evolved from natural oils to advanced techniques like high-pressure coolant systems and solid lubricants, with a strong focus on improving heat management, reducing friction, and enhancing process efficiency.
Modern lubrication cooling methods such as dry machining, MQL, and cryogenic cooling prioritize sustainability and performance, offering benefits like reduced environmental impact, lower thermal stress, and extended tool life through the strategic application of coolants.
While advancing machining performance, new lubrication technologies also address environmental and health concerns by minimizing waste, avoiding hazardous substances, and implementing sustainable alternatives like MQL with biodegradable oils.
The Evolution of Lubrication Cooling Technology
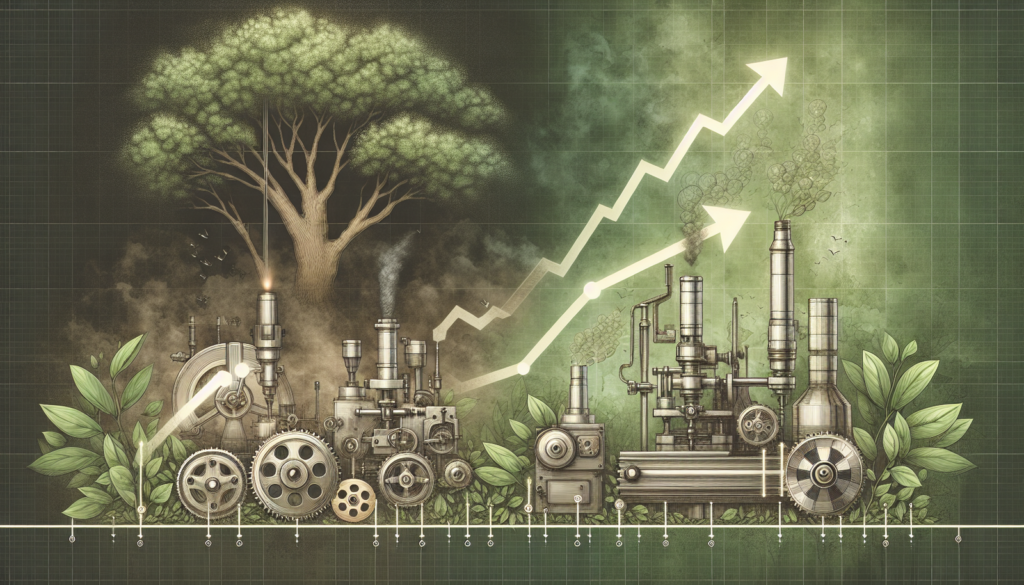
From the outset of machining operations, natural elements such as plant oils and animal fats were employed to provide cooling and lubrication during the cutting process. With the upswing in industrial activity towards the end of the 19th century, manufacturers increasingly turned to mineral oils obtained from petroleum for their lubrication and cooling needs. These mineral oils varied widely, from heavy sulfur-enriched types used in large-scale industry settings to lighter versions suited for more delicate tasks.
Advancements by mid-20th century introduced synthetic coolants aimed at maximizing the benefits derived from both oil-based substances and water. Preceding these developments in synthetic solutions were semi-synthetic coolants that emerged around 1930s, combining oil with water into an emulsion that boosted both lubricating and cooling performance significantly. To Enhance heat dissipation efficiency during machining processes, high-pressure coolant systems came into play. They utilize pressures exceeding 1,000 psi which are essential for effective chip removal along with precise temperature control.
The innovation did not cease there. The integration of solid lubricants such as molybdenum disulfide (MoS2) and graphite was a transformative step forward within this evolution. These materials have been utilized within various cutting applications to endure extreme temperatures while minimizing friction without relying heavily on liquids. Today’s diverse array of coolant formulations—including those based on water or oil coupled with specialized additives—underscores an ongoing revolution concerning how effectively we can manage thermal dynamics through advanced chemistry applied across different stages of coolant technology development.
Traditional Cutting Fluids
Flood cooling methods, which were a common practice in the application of traditional cutting fluids, utilized high volumes of fluid to achieve optimal cooling and lubrication. This approach was particularly beneficial during operations like drilling where efficient chip removal is paramount. Different types of oil-based cutting fluids included straight oils for their lubricating properties in low-duty tasks involving metals such as magnesium and aluminum. Conversely, soluble oils combined both the cooling effect and lubrication capabilities while forming a protective layer on machinery.
Advancements by the late 20th century introduced synthetic and semi-synthetic cutting fluids designed to offer superior performance across diverse industrial uses. These new formulations became especially valuable for processes that involve high-speed machining due to their ease of use, maintenance benefits, and health safety improvements resulting from lower mist production. These modern fluids were fortified with additives including phosphorus, sulfur chlorine, and boron enhancing effectiveness against heat stressors extreme conditions commonly faced during intensive machining activities.
Emergence of Sustainable Alternatives
At the turn of the century, there was a noticeable shift toward sustainable practices in the field of machining. The application of vegetable oils became increasingly popular due to their excellent lubrication properties, biodegradability, non-toxic nature, and ready availability—factors that have solidified their role in promoting sustainable machining processes. Advancements in coolant delivery techniques—including high-pressure systems and adopting environmentally friendly gases like nitrogen—have expanded opportunities for implementing more sustainable cooling strategies within the realm of manufacturing.
With its outstanding biodegradability and environmental safety credentials, palm oil has emerged as a viable replacement for traditional cutting fluids specifically within MQL (minimum quantity lubrication) machining contexts. Research efforts have been directed at fine-tuning its use so it can deliver performance levels on par with those offered by conventional fluids. These developments demonstrate how dedication to sustainability is driving innovation in both lubrication and cooling solutions across the industry dedicated to machining operations.
Advantages and Applications of Modern Lubrication Cooling Techniques

In the quest for improved sustainability, efficiency, and cost reduction in manufacturing processes, innovative lubrication and cooling strategies like dry machining, MQL (Minimum Quantity Lubrication), and cryogenic cooling are gaining prominence. These methods offer enhanced environmental benefits over traditional flood cooling techniques by complying more effectively with health safety regulations while also providing a greener footprint.
Dry machining specifically removes the need to use cutting fluids altogether, which not only results in substantial savings but also contributes positively to environmental conservation. It improves precision within the machining process due to its ability to prevent thermal shocks that can occur during intermittent cuts typical of milling operations. Alternatively, MQL involves dispensing minimal amounts of lubricant precisely at the cutting zone, which reduces both thermal stress on tools as well as coolant usage.
Employing liquid nitrogen as a coolant makes cryogenic cooling an advanced option recognized for lengthening tool life and producing superior surface finishes through excellent cooling capabilities. The strategic choice regarding selection of coolants along with their application technique must align closely with both the nature of the machining process being performed and specific requirements associated with maintaining efficient functionability of cutting tools employed therein. With consideration factors such as reduced fluid viscosity aiding chip evacuation effectiveness, there is an observed shift away from conventional flood systems towards progressive options including MQL, cryogenic solutions or possibly integrated lubri-cooling approaches.
Dry Machining
The shift toward cost reduction and environmental responsibility in the industry is well-represented by dry machining. This approach eliminates the need for metal-working fluids, leading to notable savings on expenses and positive impacts on the environment. To effectively leverage these benefits, optimization of several factors is crucial.
Selection of cutting parameters
Tool choices
Machining processes
The materials constituting workpieces
Dry machining offers a spectrum of advantages such as:
Economic effectiveness paired with environmental conservation
Increased precision in machining due to absence of thermal shock effects
Aptness for discontinuous operations like milling
Superior surface quality and extended tool life when compared with traditional wet machining methods
Minimum Quantity Lubrication (MQL)
Minimum Quantity Lubrication (MQL) is a cutting-edge method that accurately dispenses minimal amounts of lubricant as mist right to the area where cutting takes place. The goals of this technique include lowering thermal stress and tool wear, reducing coolant usage significantly, enhancing environmental sustainability and worker safety, improving the quality of surface finishes, decreasing temperatures during cutting processes, and enabling higher cutting speeds.
The effectiveness of MQL can be attributed to its exact delivery system. With digital control systems in place for MQL technology, it’s possible to fine-tune lubrication levels and flow rates efficiently. This precision leads not only to less waste but also lower energy costs thus diminishing overall manufacturing expenses. Demonstrating versatility across different substances ranging from steel and aluminum to composite materials like Carbon Fiber Reinforced Polymer (CFRP), Minimum Quantity Lubrication has been proven to provide superior surface conditions while concurrently decreasing forces exerted during cutting operations, which contributes substantially towards extending the lifespan of tools used in machining processes.
Cryogenic Cooling
Utilizing liquid nitrogen, cryogenic machining is a sophisticated cooling method that delivers numerous benefits such as:
Prolongation of tool life
Improvement in surface finish quality
Reduction in thermal deformation
Enhancement of the precision of dimensions
As it dramatically lowers temperatures within the cutting zone, this pioneering approach garners these improvements.
Cryogenic cooling provides multiple advantages during machining operations. These include:
The ability to operate at higher cutting speeds and feeds which leads to increased rates of metal removal and reduced production durations
Maintenance of the sharpness for the cutting edge contributes to an extended lifespan for tools
Decreased occurrence of adhesive wear particularly when processing materials like titanium alloys
Given these enhancements, cryogenic machining stands out for its efficiency when implemented with cryogenic cooling techniques.
Enhancing Performance with Advanced Lubrication Technologies

In pursuit of superior machining outcomes, new lubrication techniques have been introduced. The last ten years have seen a fivefold increase in the adoption of high-pressure coolant systems that deliver numerous benefits to machining processes.
Pushing coolants with force ranging from 300 to 1000 PSI
Enhancing cutting fluid penetration
Providing cooling
Offering lubrication
Solid lubricants demonstrate remarkable resistance against heat and provide intrinsic lubricative properties which aid in optimizing the performance during machining and minimizing tool wear. For example, tools made from Polycrystalline Diamond (PCD) achieve prolonged tool life along with enhanced quality in processing due to their aptness for working with particle-reinforced metal-based composites.
Augmenting cutting fluids with nano-sized particles has resulted in heightened thermal conductivity and improved effectiveness of cooling during machining operations. In parallel, advanced hybrid methods combining cooling and lubrication—like employing both carbon dioxide and minimum quantity lubrication (CO2+MQL)—have proven effective for advancing how materials such as Nimonic-80A are machined.
Nano Cutting Fluids
Nano cutting fluids are a novel type of lubricant that incorporates nanoscale particles to improve thermal conductivity and cooling performance in machining. The enhanced thermal conductivity of these cutting fluids is due to the presence of nanoparticles, which have high surface area to volume ratios and unique thermal properties.
These nano cutting fluids provide superior penetration capabilities, enabling more efficient heat removal from the cutting zone and improving tool life and workpiece quality. Studies have suggested that nano cutting fluids outperform traditional cutting fluids in reducing temperatures and improving surface finishes, especially when used with cutting tools. Yet further research is needed for a comprehensive comparison.
Hybrid Cooling/Lubrication Techniques
The fusion of cooling and lubrication methods, known as hybrid techniques, has been instrumental in improving both the environmental aspects and efficiency of machining processes. The combination of carbon dioxide with minimum quantity lubrication (CO2+MQL) is noteworthy for its capacity to significantly lower cutting temperatures, improve surface finishes, and prolong tool life—particularly when employed at elevated cutting speeds compared to conventional flood cooling.
Environmentally considerate coolants such as liquid nitrogen and carbon dioxide are beneficial due to their recyclability and minimal impact on operator health within these hybrid approaches. Studies highlight that incorporating nano-fluids into minimal quantity lubrication can be highly effective during the machining process. This has been observed while working with austempered ductile iron, but also holds promise for other materials like aluminum when using fluids based on vegetable oil.
Hybrid strategies exemplified by CryoMQL have already demonstrated success in turning operations suggesting promising extensions into CNC milling applications too. These advancements suggest a robust potential for enhancing precision across various machining operations through improved cooling and lubrication practices.
Environmental and Health Concerns
The evolution of cooling and lubrication technologies in manufacturing has led to notable improvements, but it’s also worth noting that they have not been without environmental and health implications. The conventional approach of flood cooling necessitates the use of substantial quantities of coolants, which presents challenges with disposal that are concerning for the environment as well as potential hazards for those who operate these systems. On a brighter note, Minimum Quantity Lubrication (MQL) stands out by employing biodegradable oils that don’t require biocides — mitigating environmental damage while providing a more hygienic workplace.
In an effort to align industrial practices with sustainability goals, new hybrid techniques have emerged within the realm of cooling and lubrication. These methods concentrate on reducing energy consumption, cutting down on waste generation, and contributing positively towards creating an eco-friendly landscape within manufacturing sectors. Examination into various lubrication strategies against criteria focused on sustainability—particularly health protection measures—shows that alternatives such as MQL alongside dry cutting present greater advantages from a sustainability standpoint.
Waste Management and Disposal
Traditional cutting fluids pose substantial challenges for waste management and disposal. If not handled properly, they can lead to environmental degradation through the release of various substances such as oils, emulsifiers, anti-weld agents, corrosion inhibitors, and other chemical additives. These components have the potential to negatively affect ecosystems by polluting soil and water.
In response to this problem, regulations mandate that cutting fluids undergo testing procedures aimed at confirming whether they are non-hazardous or not. The criteria used in these tests include evaluating their ignitability, corrosivity reactivity, and toxicity levels.
The Environmental Protection Agency (EPA) within the United States has put forth stringent rules pertaining to how hazardous waste should be treated,stored, and disposed of.This regulatory framework also applies to any cutting fluid categorized as hazardous.
Dry machining emerges as a solution since it avoids creating contaminated coolant from inception. Nevertheless, problems related to discarding tainted cutting liquids persist.This includes seeking eco-friendly methods for disposing mixtures of metal chips with those fluids while simultaneously mitigating risks faced by machine operators during exposure.
Despite dry machining providing an alternative method, the challenge remains when dealing with contaminated cooling liquids: identifying sustainable ways for their elimination, which may include innovations in processing blended materials consisting of metal particulates while simultaneously safeguarding machinists from contact hazards.
Health Risks for Operators
Traditional cutting fluids present various health hazards for machine operators, which include:
Lung-related illnesses such as asthma, hypersensitivity pneumonitis, chronic obstructive pulmonary disease and diminished lung functionality
Skin conditions including allergic contact dermatitis and skin irritation
An association between prior exposure to certain metalworking fluids and a heightened chance of cancer in machinists.
Fortunately, with the integration of advanced manufacturing technology processes like dry machining, these health concerns can be substantially minimized. Dry machining eschews coolants altogether, which results in a tidier work environment while also lessening incidences of respiratory issues or dermal reactions.
Minimum Quantity Lubrication (MQL) employs eco-friendly oils such as those derived from palm sources to enhance environmental sustainability while simultaneously diminishing workers’ contact with potentially dangerous chemicals.
Case Studies: Successful Implementation of Sustainable Cooling Techniques

The movement toward sustainable cooling methods in machining goes beyond academic discussion and is actively being put into practice within industrial settings. These eco-friendly strategies are becoming more prevalent in various machining processes, including mist cooling—which, though considered a green alternative to traditional flood machining, tends to produce greater surface roughness when used at elevated cutting speeds.
Exploring a couple of case studies reveals the effective application of such techniques across the machining of different materials like steel, aluminum, and specifically ti 6al 4v.
MQL in Steel Machining
In the initial scenario, employing Minimum Quantity Lubrication (MQL) in the steel machining process has proven to enhance both the surface quality and cutting performance. Specifically, this approach showed substantial improvements on factors such as workpiece surface roughness during steel processing. Research focused on hard machining of robust EN24 high-strength steel with CVD coated carbide cutting inserts using MQL indicated that it’s possible to achieve a surface finish finer than 1 m.
When integrating MQL along with mineral oil lubricants for steel material removal processes, the components fabricated exhibited a superior level of smoothness with measurements well below 1.6 m – which is considered a critical threshold for surface roughness. Incorporating environmentally benign cutting fluids like those derived from vegetable oils within the MQL strategy not only augmented machining efficiency but also concurrently minimized environmental ramifications.
Vegetable Oil-Based Fluids in Aluminum Machining
The utilization of vegetable oil-based cutting fluids, specifically olive oil, in aluminum machining was examined as part of the second case study. Olive oil served as a lubricant during the aluminum milling process and showcased its practical viability. The introduction of olive oil into the milling operations improved performance within these machining processes.
To conventional cutting fluids, lubricants derived from vegetable oils such as olive oil help lessen the environmental impact associated with machining processes. These real-life instances highlight both the compromises and factors that industries must weigh when shifting towards sustainable cooling methods.
Summary
As we’ve traversed the journey of lubrication cooling technology in machining, it’s clear that the evolution from traditional cutting fluids to more sustainable alternatives has been monumental. This shift, driven by environmental concerns and the need for improved performance, has paved the way for modern techniques like dry machining, MQL, and cryogenic cooling. These techniques, along with advanced lubrication technologies like nano cutting fluids and hybrid cooling/lubrication techniques, have significantly enhanced machining performance and sustainability. While there are environmental and health concerns associated with traditional cutting fluids, the industry is responding with innovative solutions that address these issues while improving performance. The successful implementation of these sustainable cooling techniques, as illustrated by the case studies on MQL in steel machining and vegetable oil-based fluids in aluminum machining, shows that the future of machining is indeed bright and sustainable.
Frequently Asked Questions
What are traditional cutting fluids?
Commonly utilized in machining due to their cooling and lubrication properties, traditional cutting fluids often comprise oil-based substances and employ flood cooling techniques.
What is dry machining?
Machining processes can gain environmental advantages and reduce costs by adopting dry machining, a method that forgoes the use of cutting fluids.
What is Minimum Quantity Lubrication (MQL)?
Minimum quantity lubrication (MQL) is a method that applies just enough lubricant precisely to the cutting zone, enhancing tool longevity, surface quality, and reducing environmental impact.
What are some of the health risks for operators working with traditional cutting fluids?
Workers handling conventional cutting fluids are exposed to potential health hazards that include respiratory illnesses like hypersensitivity pneumonitis and asthma, along with skin problems such as allergic and irritant dermatitis.
It is crucial to recognize and control these risks for the safeguarding of employee well-being.
What are some successful implementations of sustainable cooling techniques?
The employment of MQL (Minimum Quantity Lubrication) in steel machining and the application of fluids based on vegetable oil for aluminum machining are two examples where sustainable cooling methods have been effectively utilized. These approaches have demonstrated their efficacy by diminishing the environmental impact associated with such processes.