The manufacturing industry has been constantly evolving, giving rise to innovative technologies in the machining industry. One such technology in machining time that has gained considerable attention is high-speed cutting.
By increasing the cutting speed, the feed rate, high spindle speed, cutting speed down, spindle speeds, cutting speed up, and cutting depth, high-speed cutting technology has revitalized the machining process and enabled enterprises to carry out their production methods more efficiently and flexibly. This paper explores the advantages of high-speed cutting technology in machining and its diverse applications.

Benefits of High-Speed Machining
High-Speed Milling Can Improve Efficiency
High-speed cutting technology is a game-changer for businesses, offering numerous benefits. One of the most significant is its ability to improve production efficiency by reducing production time. Increasing the cutting speed allows the machine to complete the machining process faster, leading to a shorter production cycle. This increases delivery times, helps businesses improve their production capacity, and reduces production costs.
In addition to many benefits from this higher productivity alone, high-speed machining technology enables businesses to respond more quickly to changes in market demand. This is a crucial advantage in today’s fast-paced business environment, where rapid response times can make or break a business. By adapting to changes in demand for materials more quickly, companies can stay ahead of the competition and maintain their market position.
Increased machining accuracy
High-speed cutting technology is a game-changer in the manufacturing industry. It improves the dimensional accuracy of workpiece surfaces and ensures that machined parts meet design requirements. It does this by cutting forces, providing high speeds and a stable cutting process, which reduces machine vibration and deformation. Industries that require high precision, such as aerospace and medical device manufacturing, benefit immensely from this technology.
High-speed cutting technology has unique advantages, such as fast cutting and high cooling characteristics. It reduces the thermal effects on the material and workpiece during cutting and minimizes heat accumulation and residual heat generated by stress. This makes it easier and more difficult to cut materials and maintain the stability of the material and workpiece’s shape and size, increasing its accuracy.
In conclusion, manufacturers should adopt high-speed cutting technology. It reduces the chances of machine vibration and material deformation while increasing accuracy. Furthermore, it reduces heat accumulation and residual stress from conventional machines, making it an ideal cutting tool for industries requiring high precision.

Improvements in surface finish quality
High-speed cutting technology has revolutionized the manufacturing industry by allowing for more efficient and precise part machining. By enabling more cutting actions to be completed quickly, it reduces machine vibration and thermal deformation, improving surface finish quality and reducing surface roughness and secondary processing processes.
Through the implementation-specific operation of high-speed cutting technology tools, manufacturers can achieve higher precision cutting speeds and quality processing tool capabilities, which helps increase the overall competitiveness of manufacturing companies and their products. The benefits of high-speed cutting technology tools are straightforward: they provide enhanced productivity and quality, among many factors that make them essential tools for modern manufacturing.
Extended Tool Life
High-speed cutting technology is a game-changer for industries that rely on efficient and reliable cutting tools and parameters for production processes. By using appropriate cutting tools and parameters with high feed rates and adopting this technology, you can improve your production efficiency and extend the service life of your cutting tools. The benefits of high-speed cutting are numerous. For instance, the cutting temperature can be reduced, which reduces the cutting tool’s wear speed.
Moreover, high-speed cutting zone machining technology pays excellent attention to optimizing the cooling and lubrication systems of the cutting tool, which further enhances the tool’s wear resistance. As a result, the frequency of tool replacements is reduced, production costs are lowered, and the stability and reliability of the cutting tool wear and equipment parameters are enhanced. So, if you want to streamline your production processes and save costs in the long run, high-speed-cutting precision machining technology is worth considering.
Application field of high-speed cutting technology
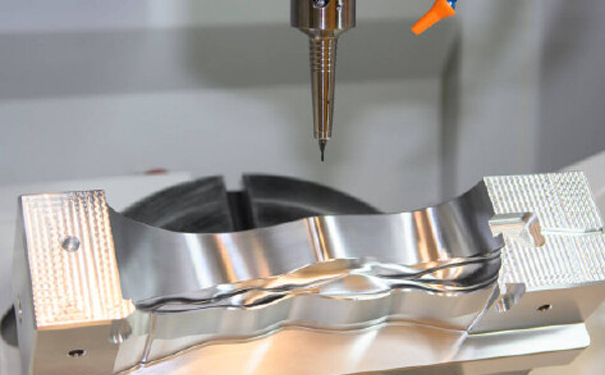
Medical Industry
In medical device manufacturing, high-speed cutting or machining is often used to process precision parts. For example, medical devices can machine metal or plastic parts more precisely through high-speed milling or high-speed machining technology, ensuring they meet large size and surface quality standards. More precision through high-speed milling or high-speed machining HSM is essential for products requiring high accuracy, such as surgical instruments and implantable medical devices.
High-speed cutting machine technology also plays a vital role in product design and rapid prototyping in the medical field. Through CNC high-speed cutting machine tools, samples and prototypes of medical devices can be quickly and accurately manufactured, accelerating product development cycles and improving flexibility, sacrificing product design quality.
Minimally-invasive surgery technology has been widely used in the medical industry, and manufacturing minimally-invasive surgical instruments have placed higher requirements on precision cutting force and high-speed machining and technology. High-speed cutting machines and technology can manufacture micro-components of minimally invasive surgical instruments, ensuring the instruments’ three-dimensional accuracy and stability.
Automotive Industry
High-speed, cutting-edge technology plays a vital role in the automotive industry. It enables the increased speed and efficiency of the manufacture of various materials for critical components such as engines, chassis, suspension systems, and brakes. This technology is particularly effective in producing complex parts, reducing production time and costs.
In automotive design and prototyping, high-speed cutting technology is crucial. By using CNC high-speed cutting machines, automotive designers can quickly create prototypes of parts, reducing the time and costs associated with traditional manufacturing methods. This allows manufacturers to accelerate the development and testing process of new models.
Furthermore, high-speed, cutting-edge technology is essential in meeting the growing demand for personalized customization in the automotive industry. With more flexibility to manufacture customized parts, automakers can cater to the individual needs of consumers who seek personalized vehicles.
Aerospace industry
High-speed cutting technology is crucial in manufacturing critical components for aircraft engines. These components, which include turbine blades, discs, compressor blades, and more, are fundamental to the engine’s performance and efficiency. High-speed cutting technology offers the best solution for a high-precision and high-efficiency machining process that ensures the quality and accuracy of these parts.
In addition to aircraft engines, high-speed cutting technology plays a vital role in producing spacecraft parts. These parts include the propulsion, control, thermal control, and other critical components. By using high-speed cutting, precise machining of lightweight materials is possible, ultimately improving the overall performance of spacecraft.
The aerospace industry demands lightweight materials to enhance fuel efficiency in aircraft. High-speed cutting technology can effectively cut at high speeds, handling lightweight composite materials, high-strength aluminum alloys, and other materials to meet the lightweight requirements of aircraft parts.
Conclusion
Applying high-speed cutting technology in machining has brought significant advantages to the manufacturing industry. By cutting parameters and improving production efficiency, tool geometry, surface quality, and tool life, this high-speed machining technology helps companies adapt to market demands and promotes the upgrading and development of the entire high-speed machining industry. In the future, with the continuous innovation and development of high-speed cutting technology, it is believed that it will play a more critical role in machining, bringing more opportunities and challenges to the manufacturing industry.