CNC (Computer Numerical Control) machining is a manufacturing process that involves using computer-controlled machines to produce precise and complex parts and components.
Suppose you are considering using CNC machining for your projects. In that case, one of the first factors you need to consider is raw material and its machining process considerations.
6 Common CNC Machining Materials
- Aluminum Alloys
- Steels
- Titanium
- Copper
- Brass
- Plastics
Let’s look at these common materials used in CNC and their associated processing considerations. Whether you are a designer or a CNC operator, this article can inspire you to select and use specific materials.
Aluminum Alloys
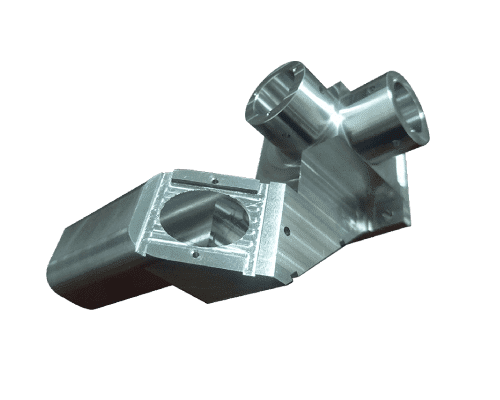
Aluminum alloys have been popular among CNC machining applications for many years due to their lightweight properties, excellent corrosion resistance, and good formability. They also come in various grades with varying properties such as strength, stiffness, and temperature resistance.
Chart of Aluminum Alloys and Applications
Aluminum Types | Properties | Applications |
Aluminum 6061-T6 | Great formability,weldability ,good strength-to-weight ratio and high Corrosion resistant.Great acceptance of Applied Coating. | Aerospace,Automotive,Sporting Goods |
Aluminum 7075-T6 | Excellent mechanical properties and exhibits good ductility, high strength, toughness, and good resistance to fatigue | Aerospace application and High Strength structure Components |
Aluminum 6060 | Wrought aluminium-magnesium-silicon family | Commonly used for architectural sections for windows, doors, curtain walls |
Aluminum 6082 | Similar composition and properties to 6061,commonly heat treated to produce tempers with a higher strength but lower ductility | Aerospace ,Automotive,Sporting Goods |
Aluminum 5083 | Great corrosion resistance Performace.Excellent performance in extreme Tough environments | Marine and industrial chemical Applications. |
Aluminum 6063 | Good hardness Levels Combined with Good formability,heat treatable and weldable | Used in Building fabrication such as window frame or door frame due to its excellent finishing qualities |
Aluminum 5052 | Exceptional corrosion resistance Performance against seawater and salt spray | Main Used in Marine Applications |
Aluminum 2024 | High strength and Weight Ratio and Good fatigue resistance,Poor Corrosion Resistance | Commercial aircraft construction or the manufacture of a host of consumer products |
Aluminum 7050 | High toughness, strength and high stress corrosion cracking resistance.Great electric conductivity Perfomance | Commercial aerospace alloy |
Aluminum MIC6 | Cast from 7000 Series Aluminum.then stress relieved to maintain dimensional stability during high-speed machining. | Suits for applications where consistent flatness and tight tolerances are critical |
Aluminum 6082-T651 | Similar composition and properties to 6061.But is commonly heat treated to produce tempers with a higher strength but lower ductility. | typically formed by extrusion and rolling |
Aluminum 2017 | heat treatable wrought alloy with intermediate strength.but harder to Machine.Workability is fair with ductility and formability better that aluminum 2014.Great Arc and resistance weldability . | Screw machine products and fittings. Pulleys and gauges. Coat hangers. Crochet and knitting needles. Rivets. General structural components. Components in transportation sector. Fasteners. |
Aluminum 7075-T651 | Excellent mechanical properties and exhibits good ductility, high strength, toughness, and good fatigue resistance .Corrosion resistant ability is better than 2000 Series. | Idea for Aircraft Parts |
What Are the Factors to be Considered for Aluminum Machining?
When you choose an aluminum alloy as your product material for a CNC machining project, you may consider the below factors for smooth production and good product functions.
Raw material properties
- Strength: Aluminum alloy’s strength determines how much force it can withstand before deforming or failing. It also influences the cutting speed used during machining.
- Ductility: Ductility measures how well a material can stretch and deform without breaking. Higher ductility allows for greater tolerance and improved surface finish during roughing operations.
- Corrosion Resistance: Aluminum alloy’s corrosion resistance determines how well it holds up to harsh environmental conditions like saltwater or chemical exposure. High corrosion resistance will help ensure the part retains its intended function when exposed to these elements.
- Heat Treatability: Heat treatability affects aluminum alloy’s mechanical properties, such as strength and hardness. This makes selecting a material type with the correct heat-treatable characteristics for your application needs important.
By considering these fundamental material properties when selecting an aluminum alloy for your machining operations, you can ensure optimal performance and quality results from your parts.
Product Design Features
- Dimensions: To minimize tool chatter, allowances should be included for shrinkage due to machining operations. Additionally, knowing the exact dimensions of your part before machining will ensure an accurate fit with other components in your final assembly.
- Clearance: Ensuring adequate clearance spaces between adjacent parts will prevent interference between moving pieces during machining. This prevents damage to the details being worked on and the cutting tools being used.
- Tolerances: When specifying tolerances for your parts, consider the size and complexity and any additional operations, such as heat treatment or surface finishing, that may be necessary. Properly determining these parameters can save time and costs during production.
- Finishes: The right choice of finish for an aluminum alloy part depends on its intended application, corrosion resistance requirements, and aesthetics desired by customers. Various finishes are available, including brushing, polishing, passivating, or anodizing treatments, which all offer different levels of corrosion protection and decorative value.
3. Machining Guide for Aluminum Alloys
- Tool Selection: Choosing the right cutting tools for aluminum alloy machining will help ensure an optimal finish and reduce tool wear. High-speed steel (HSS) and carbide tools are typically used with an aluminum alloy, depending on the application.
- Feed Rates: Using appropriate feed rates for your operation will produce optimal performance and part quality. Too rapid of a feed rate can cause excessive wear on the tools, while too slow of one can lead to poor surface finish or even breaking of the tool itself.
- Coolant: The use of coolant is essential for successful machining operations with aluminum alloys as it helps carry away heat generated by the cutting process, cooling both the workpiece and tooling. It also helps flush away chips and debris from the work area, improving visibility during machining.
- Clamping Force: Make sure that parts are securely clamped into place before machining to prevent movement or vibration during operations which could damage both the part and cutting tools used.
Steels
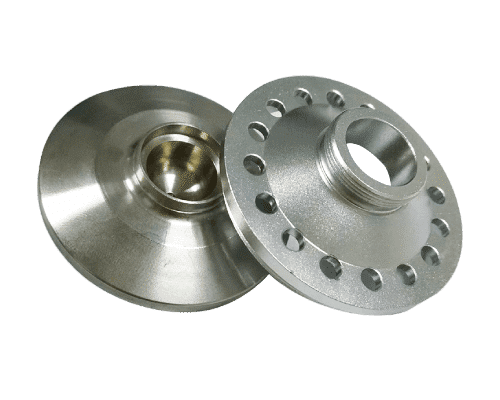
Steel is a solid yet versatile material used in many industries, from automotive parts to medical implants. Steel can be processed using various techniques, including grinding, milling, turning, tapping, drilling, etc.
Steel can be difficult to machine due to its high heat conductivity, so choosing the right cutting tools and coolant is important when working with steel. In addition, steels tend to be more prone to work hardening, so proper feeds and speeds must be followed during the machining process.
Chart of Steels and Applications
Stainless Steel Types | Properties | Applications |
Stainless steel 304 | Easy to Machining and can be Formed in Various Shapes.Featured with Excellent Machanical Properties and higher corrosion resistance. | Household and industrial applications such as food handling and processing equipment, screws,machinery parts, utensils, and exhaust manifolds |
Stainless steel 316 | Similar mechanical properties to 304, but it has higher corrosion resistance due to the addition of 2% molybdenum alloy | Marine and offshore applications. |
Stainless steel 303 | 303 has more roughness than 304, but lower Corrosion resistance due to the addition of sulfur | Suits for Mass Production.Cost-effective and Shorten your Lead Time. |
Stainless Steel 17-4 PH | A precipitation hardening stainless steel.it is capable of being hardened up to 44 Rc.Featured with excellent corrosion resistance. | Petroleum and chemical industries, as well as use in aircraft parts |
Stainless steel 416 | It is well-known as it free-machining. It has the largest machinability of all stainless steel grades. moderate corrosion | Automatic screw machined parts Washing machine parts Valve parts Gears Pump shafts Motor shafts Studs Bolts and nuts |
Stainless steel 2205 Duplex | Combined austenitic alloy’s resistance to stress corrosion cracking and high strength, With the good machinability of ferritic alloy. | Suits for parts in high chlorine environments: marine vessels, chemical Processing. |
Stainless steel 430 | Magnetic and corrosion resistant.Similar features as 304 stainless.Due to lack of Nickel,430 has lower Corrosion resistant ability but Better Price. | Chemical Process,Petrochemical |
Stainless steel 301 | Stainless steel 301 is corrosion resistant similar to Stainless steel 304. | Air frame sections Highway trailer components Automotive wheel covers Wiper blade clips and holders Stove element clips Screen frames Toaster springs Curtain walls |
Stainless steel 15-5 | Higher toughness than 17-4 , better corrosion resistance and transverse properties compared to other similar martensitic grades. | Hollow shafts. Engine parts. Sections of marine gas turbine compressors. Papermill equipment. Gears. Aircraft components. Nuclear reactor components. Fittings and fasteners. |
Stainless steel 420 | A hardenable, martensitic stainless steel that is a modification of Alloy 410.Better Toughness and Corrosion resistant features due to the Carbon and Chromium Elements. | Used for a variety of applications where good corrosion and outstanding hardness is necessary. |
What Factors Should be Considered in Steel Processing?
The following details should be considered when selecting steel as the part material for CNC machining.
- Steel Properties:
- Chemical composition: Different steels have different ratios of elements like carbon, manganese, phosphorus, and sulfur, which can determine how easy it is to machine them.
- Heat Treatability: Heating and cooling steel can affect its grain structure, affecting machinability.
- Hardness: Harder steels are more difficult to machine due to increased cutting forces and decreased chip formation.
- Tensile Strength: Higher tensile strength can increase cutting forces, reduce chip formation, and decrease tool life.
- Yield Strength: Higher yield strength can make steel more challenging to cut due to increased binding between the chip and workpiece.
- Elongation: Lower elongation rate can increase cutting forces and reduce surface finish.
- Hardenability: Harder steels are more difficult to machine due to increased cutting forces and decreased chip formation.
- Product Design Features:
- Hardness: The hardness of a material affects the cut’s speed and wear on the cutting tool. Softer materials can be machined more quickly but may require frequent tool changes due to increased wear.
- Internal&External radii: Internal radii should be kept as small as possible to minimize cutting forces, improve surface finish, and reduce tool wear.
- Draft angle: Draft angles help with the release of chips during machining, which can help with surface finish and prolong tool life.
- Tolerances: Dimensional tolerance must be considered when designing a part to ensure it can be machined accurately within the given tolerances.
- Chamfers: Chamfers help reduce cutting forces by allowing chips to separate more easily from the workpiece, resulting in better surface finishes.
Major Processing Considerations for Different Steels
Machining considerations can vary significantly depending on the type of steel being machined. Some of the critical factors that need to be taken into account when machining steel include its composition, hardness, and toughness.
Here are some general machining process considerations for different types of steels:
- Carbon Steel: Carbon steel is a relatively soft material that is easy to machine. It is also relatively inexpensive, which makes it a popular choice for many machining applications. However, it can be prone to distortion and warping during the machining process, so careful attention needs to be paid to the cutting speed, feed rate, and coolant flow.
- Stainless Steel: Stainless steel is harder than carbon steel and can be more challenging to machine. It is also prone to work hardening, which means that the material can become even harder and more difficult to machine as the cutting process progresses. As a result, stainless steels require slower cutting speeds, more coolant, and more frequent tool changes.
- Tool Steel: Tool steel is a hard, wear-resistant material often used for cutting tools and other high-stress applications. It requires high cutting speeds, low feed rates, and plenty of coolants to prevent overheating and damage to the cutting tool.
- Alloy Steel: Alloy steel contains one or more alloying elements, such as nickel, chromium, or molybdenum, that can significantly impact its machinability. Generally, alloy steel requires lower cutting speeds and higher feed rates than carbon or stainless steel. However, the specific alloying elements and their concentrations can impact the optimal machining process parameters.
In addition to these factors, other considerations include the geometry of the workpiece, the machining operation (e.g., turning, milling, drilling, etc.), and the cutting tool being used. Consultation with a machinist or a manufacturer’s data sheet may be necessary to determine the best machining process parameters for a specific steel alloy.
Titanium
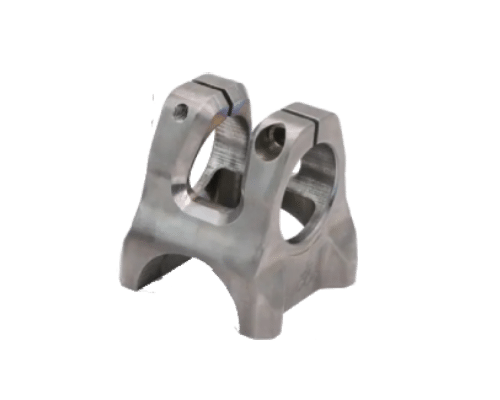
Titanium is a strong, lightweight metal in many high-performance applications, such as aerospace, medical implants, and military equipment. When machining titanium using a CNC machine, there are several considerations to keep in mind to achieve the best results:
- Machining Parameters: Titanium is difficult to machine due to its low thermal conductivity and high reactivity with cutting tools. It is essential to use appropriate cutting parameters, such as cutting speed, feed rate, and depth of cut, to prevent tool wear and work hardening of the material.
- Tooling: When machining titanium, it is important to use appropriate cutting tools to achieve the best results. Carbide tools with high cobalt content are commonly used for titanium machining due to their high hardness and wear resistance. Other materials, such as ceramic or polycrystalline diamonds (PCD), may also be used for specific applications.
- Lubrication: Titanium can be prone to overheating and galling during machining, so it is essential to use appropriate lubrication to reduce friction and heat buildup. Cutting fluids, such as oils or emulsions, can improve tool life and achieve a better surface finish.
- Workholding: Due to its low thermal conductivity, titanium can be prone to warping or distortion during machining. It is important to use appropriate work holding to ensure the part remains stable during the machining process.
- Post-processing: After CNC machining, titanium parts may require post-processing to achieve the desired surface finish or other properties. This can include polishing, passivation, or other finishing processes.
Overall, titanium is challenging to machine using CNC machines, but it is possible to achieve high-quality results with appropriate tooling, lubrication, and machining parameters. Working with experienced machinists and using specialized cutting tools is essential to achieve the best results when machining titanium.
Copper
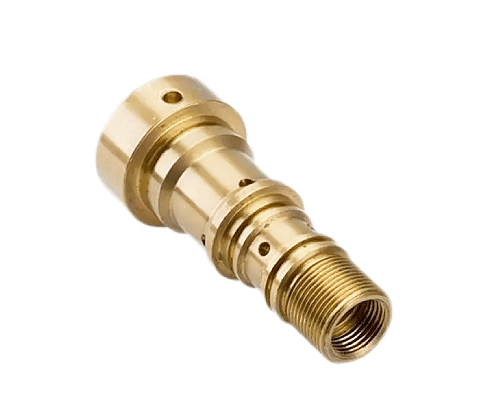
Copper is a highly conductive metal used in various applications, including electrical and electronic components, plumbing fixtures, and decorative objects. When machining copper using a CNC machine, there are several considerations to keep in mind to achieve the best results:
- Machining Parameters: Copper is a soft metal that can be machined quickly and is prone to built-up edge formation and galling. It is essential to use appropriate cutting parameters, such as cutting speed, feed rate, and depth of cut, to prevent these issues and achieve the desired surface finish.
- Tooling: When machining copper, it is important to use appropriate cutting tools to achieve the best results. Carbide tools are commonly used for copper machining due to their high hardness and wear resistance, but high-speed steel (HSS) tools can also be used for low-volume applications.
- Lubrication: Copper can be prone to overheating and galling during machining, so it is essential to use appropriate lubrication to reduce friction and heat buildup. Cutting fluids, such as oils or emulsions, can improve tool life and achieve a better surface finish.
- Electrical Conductivity: Copper is a highly conductive metal, so it is essential to consider the electrical conductivity of the part being machined. If the piece is intended to be used in an electrical or electronic application, it is important to avoid damaging the surface finish or altering the material’s conductivity.
- Post-Processing: After CNC machining, copper parts may require post-processing to achieve the desired surface finish or other properties. This can include polishing, deburring, or other finishing processes.
Overall, copper is a relatively easy material to machine using CNC machines, but it is important to consider the above factors to achieve the best results. With appropriate tooling, lubrication, and machining parameters, it is possible to achieve high-quality results when machining the copper
Brass
Brass is a popular material for CNC machining due to its good machinability, attractive appearance, and relatively low cost. When machining brass using a CNC machine, there are several considerations to keep in mind to achieve the best results:
Machining Parameters: Brass is a soft metal that can be machined quickly and is prone to annoying and built-up edge formation. It is important to use appropriate cutting parameters, such as cutting speed, feed rate, and depth of cut, to prevent these issues and achieve the desired surface finish.
Tooling: When machining brass, it is important to use appropriate cutting tools to achieve the best results. Carbide tools are commonly used for brass machining due to their high hardness and wear resistance, but high-speed steel (HSS) tools can also be used for low-volume applications.
Lubrication: Brass can be prone to overheating and galling during machining, so it is important to use appropriate lubrication to reduce friction and heat buildup. Cutting fluids, such as oils or emulsions, can improve tool life and achieve a better surface finish.
Part Design: The design of the part being machined can also affect the machining process. It is important to consider the part’s geometry, tolerances, and surface finish requirements when designing for CNC machining to achieve the desired results.
Post-processing: After CNC machining, brass parts may require post-processing to achieve the desired surface finish or other properties. This can include polishing, deburring, or other finishing processes.
Overall, brass is a relatively easy material to machine using CNC machines, but it is important to consider the above factors to achieve the best results.
Plastic
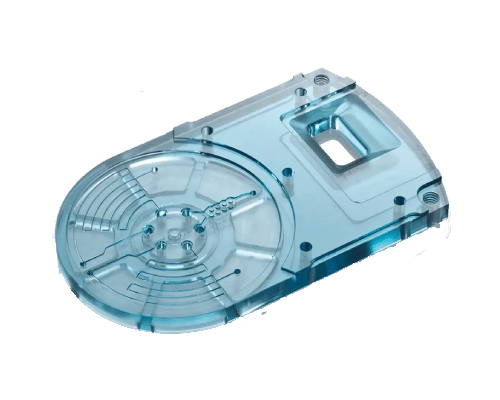
Plastics offer many advantages for CNC machined parts, including low cost, lightweight properties, and good chemical resistance. Plastics are easy on tools, but they require special techniques when machining due to their tendencies toward melting or sticking if not adequately cooled during processing steps like drilling or milling operations.
Many different types of plastic materials are suitable for CNC machining. Here are some of the most common plastics used in CNC machining:
- Acetal (Delrin): Acetal is a thermoplastic material with high stiffness, low friction, and good dimensional stability. It is commonly used for precision parts and gears.
- Acrylic (PMMA): Acrylic is a transparent thermoplastic material often used for display applications, such as signage, point-of-sale, and light diffusers.
- Polyethylene (PE): Polyethylene is a low-cost thermoplastic material with good chemical resistance and electrical insulation properties. It is commonly used for packaging, piping, and electrical insulation.
- Polypropylene (PP): Polypropylene is a thermoplastic material with high chemical resistance, good fatigue resistance, and low friction. It is commonly used for packaging, medical devices, and automotive parts.
- Polycarbonate (PC): Polycarbonate is a transparent thermoplastic material with high impact resistance, good dimensional stability, and good electrical insulation properties. It is commonly used for safety goggles, face shields, and automotive components.
- Nylon (PA): Nylon is a thermoplastic material with high strength, toughness, and wear resistance. It is commonly used for gears, bearings, and other high-stress applications.
- PEEK (Polyetheretherketone): PEEK is a high-performance thermoplastic material with high-temperature resistance, chemical resistance, and mechanical strength. It is commonly used for aerospace, automotive, and medical applications.
Machining Process Considerations(Plastics)
When CNC machining the plastic material, it is important to use appropriate cutting tools and techniques to ensure that the material is cut cleanly and efficiently. The optimal machining parameters, such as cutting speed, feed rate, and coolant, will depend on the specific plastic material being machined and the application requirements. Working with an experienced CNC machining service provider can help ensure that the optimal machining parameters are used for the specific plastic material and application.
Conclusion
When selecting your materials for CNC machining projects, it’s important to consider which type of material and their associated processing considerations. From aluminum alloys that require chip evacuation control to plastics that must be cooled during cutting operations – each material has its own unique set of requirements that must be considered when designing a part for production on a CNC machine, and proper tool selection and cutting strategies. Coolant use can help to ensure successful machining. By understanding these processing considerations beforehand, you can ensure that your part will run smoothly through production without any issues or delays in delivery time!
You may have a question, ” How to quickly select the suitable material without comparing material costs? Stcnc Machining can help your CNC machining project at the design stage by suggesting materials, quotation options, and design machinability evaluation.