Introduction: “Hardcore” in the CNC machining
Materials such as aluminum alloys, copper, and plastics may be familiar in CNC machining. Still, the situation can be completely different when it comes to titanium alloys, nickel-based superalloys, or hardened steels. Advanced CNC machines are crucial for machining these difficult materials as they enhance precision, improve machining efficiency, and mitigate errors. Imagine trying to cut a titanium alloy, and you may find that the cutting tool wears out faster than expected, heat builds up quickly in the cutting zone, and you may even experience vibration and chatter, all of which can have a severe impact on the quality of the final product. So, how can we effectively deal with these “hard bo “es”? This “article will discuss the material properties, tool selection, cutting parameters, coolant application, vibration control, tool wear monitoring work hardening, and surface finish, which are seven key aspects of a comprehensive analysis.
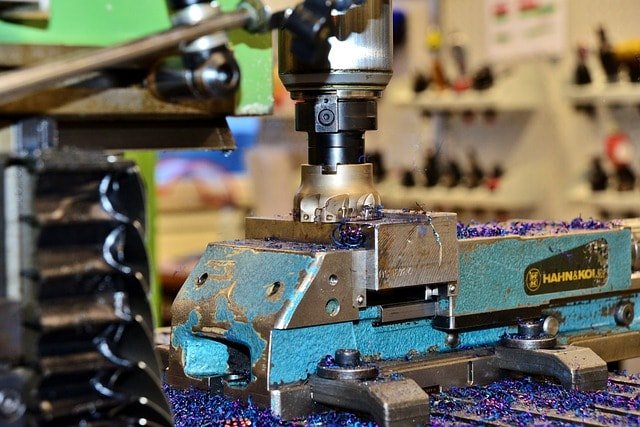
What are the more difficult materials to work with?
Some materials are considered difficult to machine in machining due to their unique physical and mechanical properties. These materials are usually characterized by high hardness, high strength, high-temperature resistance, or exceptional chemical stability. They are widely used in demanding applications such as aerospace, energy, and medical devices.
A CNC machine faces unique challenges when machining these difficult materials, emphasizing the importance of precision, tool selection, and managing the cutting zone to optimize performance and overcome common machining difficulties.
The following are some typical hard-to-machine materials:
1. Titanium Alloys
Overview: Titanium alloys are known for their excellent strength-to-weight ratio and corrosion resistance, especially in aerospace and biomedical applications. They maintain strength at extreme temperatures and are also highly fatigue-resistant.
Application areas: Mainly used in aircraft engine components, orthopedic implants, chemical equipment, etc.
2. Nickel-based superalloys
Overview: Nickel-based superalloys (e.g., Inconel, Hastelloy) are very resistant to heat and oxidation and maintain excellent mechanical properties at high temperatures. These alloys are commonly used where high strength and corrosion resistance are required.
Applications: Widely used in gas turbine engines, nuclear reactors, and heat-resistant components in the oil and gas industry.
3. Hardened steels
Overview: Hardened steels are steel grades that have had their hardness and strength increased by a heat treatment process. They are commonly used for the manufacture of wear-resistant and highly loaded components such as molds, tools, and bearings. They have a very high surface hardness and can withstand extreme working conditions.
Areas of application: Mold and die-making, tool-making, machine parts, etc.
4. stainless steel
Overview: Stainless steels (e.g., 304, 316 stainless steel) are known for their corrosion resistance and high strength. They are particularly suitable for use in wet or corrosive environments. They also have good ductility and weldability.
Applications: Commonly used in food processing equipment, medical devices, construction materials, and chemical equipment.
5. Composite materials
Overview: Composite materials (e.g., Carbon Fiber Reinforced Polymer (CFRP) combine the advantages of various materials, such as high strength, lightweight, and corrosion resistance, and are used in many applications where high performance and lightweight are required.
Applications: Widely used in aerospace, racing cars, wind turbine blades, and sports equipment.
6. Tungsten
Overview: Tungsten alloys have extremely high densities and melting points, making them ideal for use in extreme environments, especially at high temperatures and pressures. Their high density also makes them valuable in specialized applications.
Applications: Commonly used in ballistic materials, high-temperature molds, and protective devices in the aerospace industry.
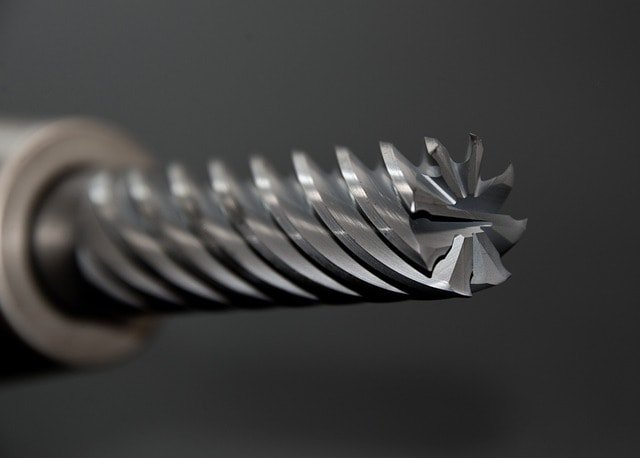
1. Understanding Material Properties
Challenge: Difficult materials often exhibit high hardness, toughness, and heat resistance. These properties can cause rapid tool wear, increased cutting forces, and difficulty maintaining tight tolerances.
Tip: Start by thoroughly understanding the materials. For example, titanium alloys have low thermal conductivity, meaning heat tends to concentrate at the cutting edge, increasing wear. On the other hand, nickel-based superalloys are prone to work hardening, which can make subsequent passes even more challenging and affect the material removal rate. Additionally, understanding the manufacturing process is crucial to achieve the desired precision and quality.
2. Tool Selection and Geometry
Challenge: Standard cutting tools may not withstand the high forces and temperatures involved in machining rigid materials, leading to premature wear or tool failure.
Tip: Select cutting tools specifically designed for complex materials. Specialized cutting tools made from carbide or ceramics are typically preferred for their hardness and heat resistance. Tools with advanced tool coatings like TiAlN (Titanium Aluminum Nitride) or diamond-like carbon (DLC) should be considered to reduce friction and enhance tool life. The tool’s design is also critical—opt for tools with a positive rake angle to reduce cutting forces and minimize work hardening.
3. Optimizing Cutting Parameters
Challenge: Using inappropriate cutting speeds, feed rates, or depths of cut can exacerbate tool wear, lead to poor surface finish, and even cause part deformation.
Tip: Carefully optimize your cutting parameters. For example:
Cutting Speed: Lower cutting speeds are often necessary to reduce heat generation. Speeds between 30-50 m/min are recommended for titanium alloys.
Feed Rate: A moderate feed rate helps balance tool life and material removal rate. Too low a feed can increase heat concentration, while too high can overload the tool.
Depth of Cut: Start with shallow depths of cut to minimize tool load and reduce the risk of deflection or vibration, which is particularly important in materials prone to work hardening.
Selecting optimal cutting strategies, such as adjusting cutting parameters and tool coatings and implementing high-speed machining, is crucial to minimizing material damage and enhancing machining efficiency.
4. Coolant Application
Challenge: Managing heat during machining is critical, as excessive heat can cause thermal expansion, affect part tolerances, and accelerate tool wear.
Tip: Use high-pressure, directed coolant to remove heat from the cutting zone efficiently. Flood or high-pressure coolant delivery systems benefit materials like Inconel and titanium. Consider using coolant with anti-corrosive properties to protect the workpiece and the machine.
5. Vibration Control
Challenge: High cutting forces and hardness of difficult materials can cause vibrations, leading to chatter, poor surface finish, and reduced tool life.
Tip: Implement vibration control techniques such as:
Stable Fixturing: Ensure that the workpiece is securely clamped to minimize movement.
Tool Length: Use the shortest possible tool length to reduce deflection.
Machine Damping: Consider using machine tools with built-in damping systems or applying external vibration dampers.
6. Monitoring Tool Wear and Tool Life
Challenge: Tool wear is more rapid and unpredictable when machining complex materials, leading to potential issues like dimensional inaccuracy and poor surface integrity.
Tip: Regularly monitor the wear of your machining tools using advanced techniques such as in-process sensors or visual inspection. Implementing a tool wear compensation strategy in your CNC program can help maintain part quality. It’s also possible to have spare tools ready for quick replacement to minimize downtime.
7. Work Hardening and Surface Finish
Challenge:
Materials like nickel-based superalloys are prone to work hardening, where the material becomes more challenging as it is machined, making subsequent cuts even more difficult.
Tip:
To minimize work hardening:
Use sharp tools and replace them frequently.
Where possible, opt for higher feed rates to reduce the number of passes.
Consider using a small depth of cut to avoid excessive heat buildup.
Optimize your cutting conditions and tool geometry for surface finish to reduce surface roughness. Additionally, post-machining processes such as polishing or surface treatments should be considered to achieve the desired finish. Achieving the desired surface finish in small-part machining is crucial; using specific cutting tools and techniques can enhance surface quality and optimize machining parameters. Selecting the proper CNC machining method is essential to enhance the quality and efficiency of manufacturing processes.
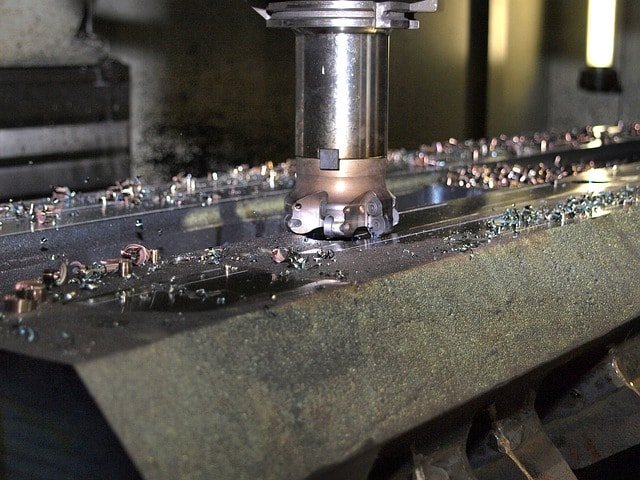
Conclusion
Machining difficult materials with CNC technology requires a strategic approach considering material properties, tool selection, cutting parameters, coolant application, vibration control, and tool wear monitoring. By understanding and addressing these challenges, you can significantly enhance your machining operations’ accuracy, accuracy, and quality. Understanding the CNC machining process and its critical steps is essential to transform a digital design into a high-precision metal part, ensuring high precision and quality. With careful planning and execution, even the most challenging materials can be machined to meet the high standards required in critical applications.