Introduction
In modern manufacturing, the demand for automation and intelligent processing technology is increasing, especially in designing and manufacturing complex parts, and 3D models combined with machine learning bring new possibilities for identifying machining difficulties. Through advanced machining feature recognition and computer vision techniques applied to identify defects in manufacturing processes, engineers can effectively analyze and predict difficult points in the machining process to choose processing paths and methods more intelligently. The deep learning method enhances traditional defect detection approaches by offering better accuracy and efficiency in analyzing large datasets. This article will explore combining 3D models and machine learning techniques (such as deep learning models) to identify features and optimize traditional machining processes.
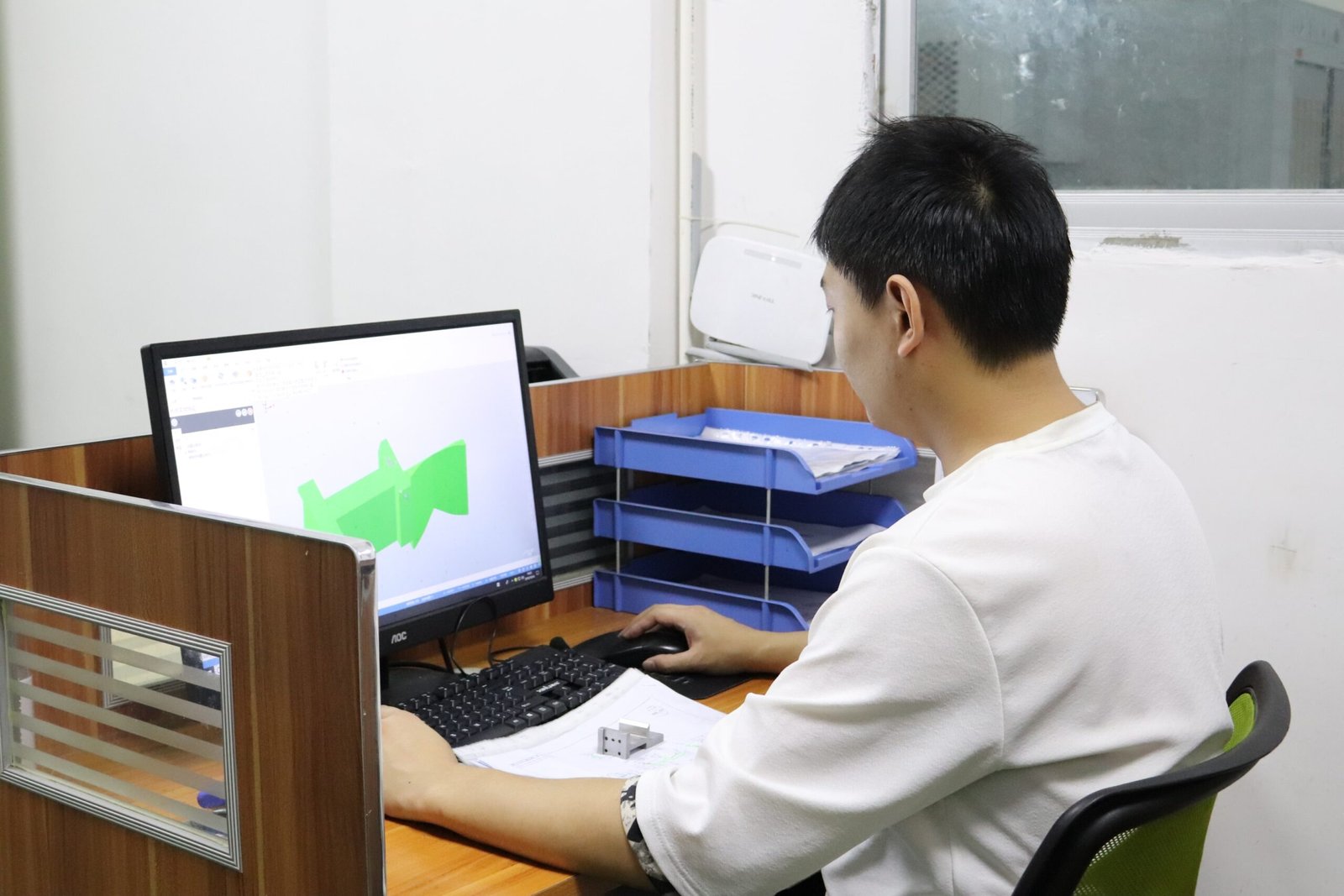
What is a 3D model? Its importance in processing inspection
A 3D model is a three-dimensional product image created by CAD software, which can accurately display the product’s geometric structure, size, Angle, and spatial relationship. Unlike traditional two-dimensional drawings, 3D models can present the complete product picture from all angles, helping engineers gain insight into design intent and product details. The importance of processing testing is reflected in the following aspects:
More accurate shape and size presentation: 3D models allow designers and engineers to more intuitively understand product shapes and avoid misreading complex structures hidden in two-dimensional drawings.
Early problem troubleshooting: 3D models can simulate machining conditions in advance through virtual simulation, helping engineers identify problems and develop more appropriate processing strategies.
Optimizing the process flow: The 3D model provides a more scientific basis for selecting the processing path and planning the process flow, thus reducing unnecessary trial and error in actual production.
The role of machine learning in machining feature recognition
Traditional feature recognition methods rely on rules and algorithms and often have poor complex or irregular feature recognition results. By introducing deep learning technology, feature recognition methods can be significantly enhanced, making them more accurate and efficient. Machining features-based recognition and classification using deep learning methods involves the development of advanced algorithms that utilize feature descriptors and CNN models to identify machining features accurately. Machine learning models can learn the shape and pattern of features from large amounts of 3D model data to accurately classify and label new models.
Deep learning model and machining feature recognition
Deep learning models, such as convolutional neural networks (CNNS) and recurrent neural networks (RNNS), can play an essential role in the feature recognition of 3D models. CNNS are particularly suited for processing image data and can scan different areas in 3D models to automatically classify specific geometric shapes into different processing features. RNNS are good at processing sequence information and are very effective for identifying the constituent structure of complex features.
This deep learning-based feature recognition method does not rely on manually set rules but learns large amounts of data to discover potential feature relationships. This method improves identification accuracy and significantly reduces the processing preparation time, thus providing practical support for intelligent manufacturing.
Application of machine learning to identify traditional machining processes
Deep learning models are also widely used in identifying conventional machining processes. For example, for parts with a lot of drilling and grooving, the machine learning model can automatically recognize these features and recommend the corresponding machining method (such as drilling, milling, or turning), thereby intelligentizing the machining process. This method is especially suitable for the processing path planning of complex workpieces, which can significantly reduce human intervention and improve processing efficiency.
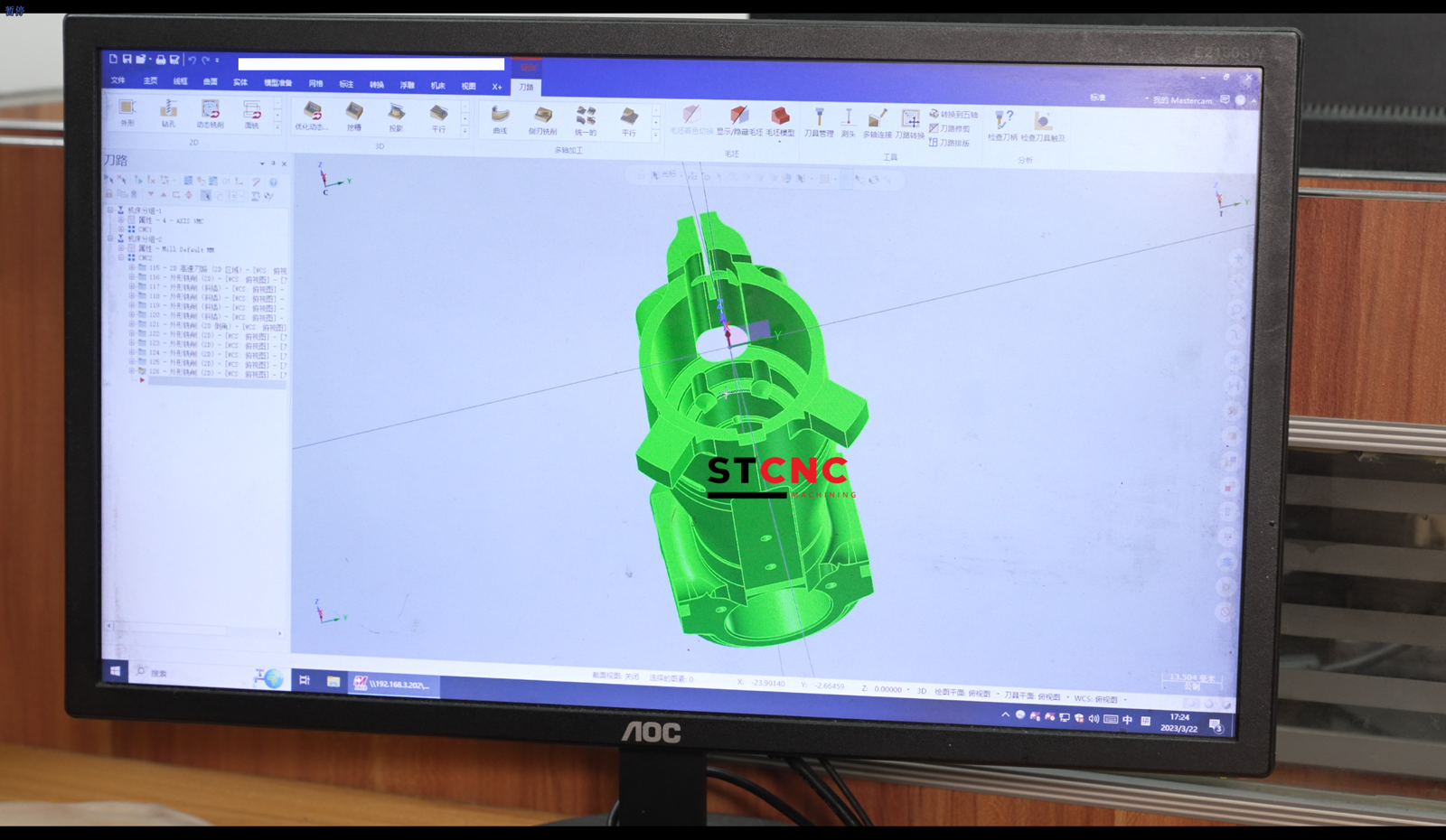
Data Generation and Preprocessing
Any data-driven machine learning algorithm’s performance heavily relies on the quality of the data. In machining feature recognition, having a balanced and comprehensive training dataset is crucial for achieving the best accuracy and robustness of the model. This study generated an extensive dataset comprising 119,320 3D CAD models, each annotated with eight distinct machining features, including holes, slots, steps, chamfers, and rounds.
To ensure the model’s effectiveness, the dataset was meticulously divided into three sub-datasets for learning, validation, and testing, adhering to a 75:25 ratio for training and testing, respectively. This division helps fine-tune the model and validate its performance on unseen data. We employed 1-bit bools and 32-bit integers for voxels and labels to efficiently manage the large data size. Additionally, the chunk size was optimized based on the voxel resolution, and the data were compressed using the gzip method. These preprocessing steps are essential to streamline the data handling and enhance the model’s training efficiency.
How to detect machining difficulties through 3D models and machine learning
Build a processing feature database.
Engineers can first collect many 3D models with processing annotations in practical applications to form a processing feature database. These databases can include a variety of 3D models with different features and label the processing process corresponding to each feature. After the database is input into the machine learning model, the model will be able to identify the corresponding relationship between different geometric features and processing technology through the training and learning of the model.
Automatic recognition of processing features using a deep learning model
In the machining process, the geometric features in the 3D model are an essential basis for selecting the machining path and tools. The system can scan the entire 3D model using deep learning models and automatically identify machining features. For example, the model can identify difficult-to-machine areas such as small holes, threads, or irregular surfaces in part and assess possible machining problems in advance to detect defects. Additionally, detecting defects using advanced technologies and methodologies, such as machine vision and ultrasonic techniques, can significantly enhance quality control. These analyses can help engineers develop optimal processing strategies.
Real-time monitoring and feedback
Deep learning models can also be used to monitor processes in real time. For example, in five-axis machining, the system can monitor the tool path through 3D models and machining data to detect possible collisions or overcuts. At the same time, by combining real-time monitoring with machining feature recognition, the system can adjust the tool path or machining parameters at any time according to the machining progress, improving the machining accuracy and efficiency.
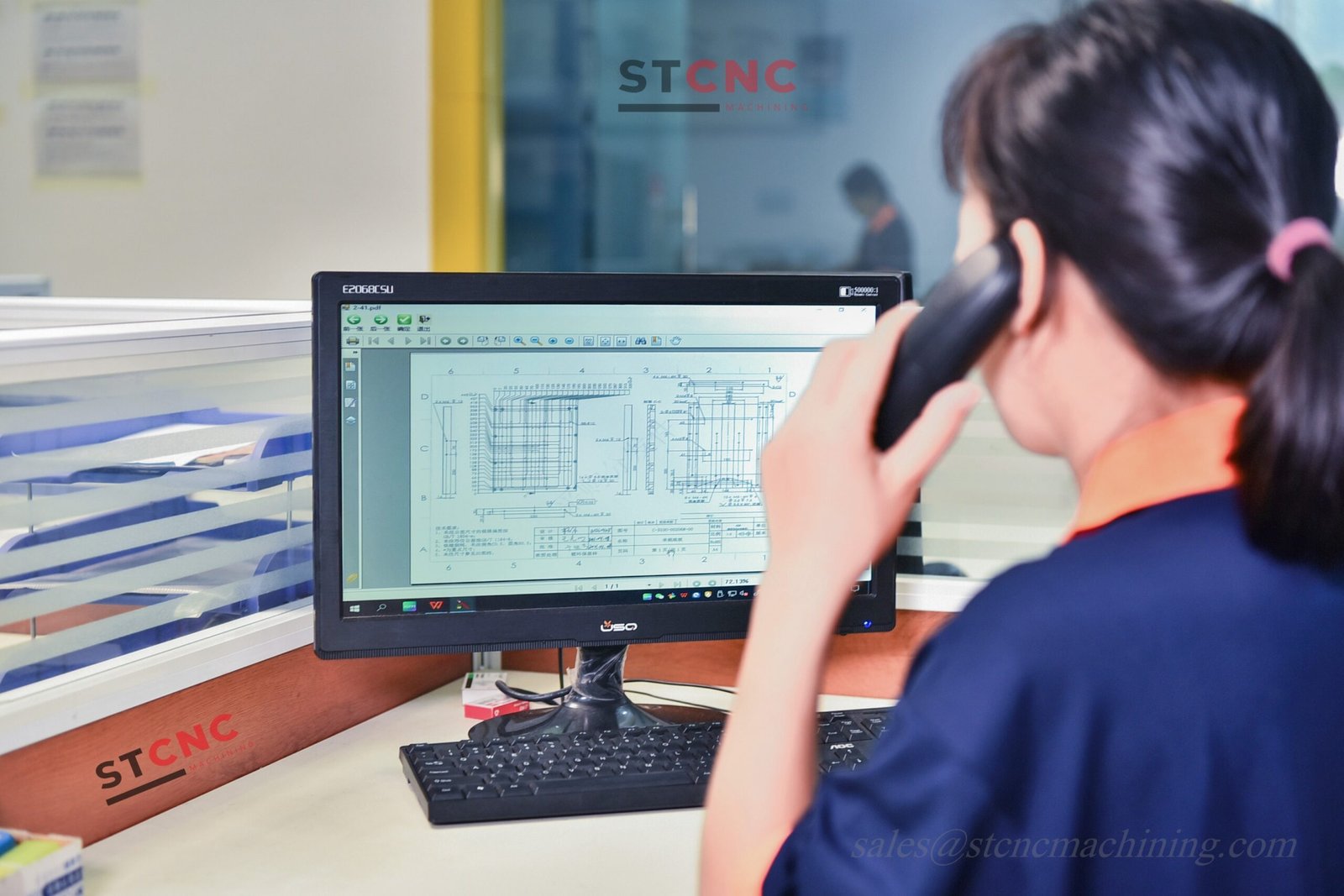
Application of 3D model, deep learning, and machining feature recognition in different machining processes
Identification application in drilling processing
When drilling parts, engineers can identify the location, size, and number of holes through 3D models, which can be automatically analyzed by deep learning models. For example, through feature recognition, the system can identify parts that require multiple drilling and select the right drilling tool and speed to optimize the entire drilling process.
Optimization of milling processing
Combining 3D models and deep learning models can identify difficult-to-process areas such as bumps and grooves in milling complex geometric parts. The system can optimize the path during machining and reduce tool wear rates through automatic path planning and real-time monitoring.
Application in turning processing
In the turning process, the system can identify the suitable machining area according to the part’s rotation characteristics and automatically plan the cutting depth and feed speed to ensure the stability and efficiency of the processing.
Future development of deep learning models in 3D processing feature recognition
The development prospects for deep learning and 3D machining feature recognition in mechanical engineering are vast. In the future, with the accumulation of data and the advancement of algorithms, deep learning models can further improve the accuracy of feature recognition and achieve more complex and efficient automated processing processes. At the same time, combined with augmented reality (AR) technology, engineers will be able to view 3D models and feature recognition results directly in the field, further simplifying operations.
Case Study: Machining Tool Identification
Machining tool identification is a pivotal task in manufacturing systems, and the use of 3D point clouds has become increasingly popular for this purpose. Traditional machine learning techniques, however, often fall short when dealing with the complexity of point cloud data. In this study, we propose a novel approach that leverages 3D point clouds and deep learning to identify machining tools with high precision.
Our method involves extracting temporal point clouds from a workpiece in progress and training a deep learning model to classify the tools used. This approach handles the intricacies of point cloud data and achieves remarkable accuracy. Specifically, our deep learning model attained a classification accuracy of 98.81% at the 79th epoch, demonstrating its effectiveness in identifying machining tools. This high level of accuracy underscores the potential of deep learning in revolutionizing tool identification in intelligent manufacturing systems.
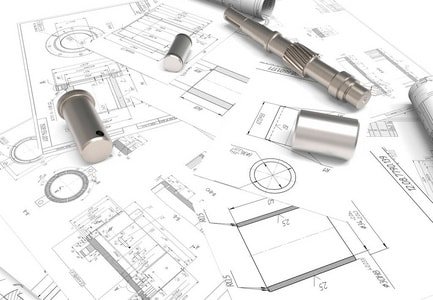
Evaluations and Results
The proposed MPI system was rigorously evaluated using a dataset of 119,320 3D CAD models, each annotated with eight machining features. The system demonstrated impressive performance, achieving over 98% accuracy in identifying a part’s manufacturability and approximately 98% accuracy in identifying the manufacturing processes of synthesized workpiece models.
These results highlight the system’s effectiveness in discerning machining processes and manufacturability from CAD models. The high accuracy rates suggest that the system can be a valuable tool in various applications, including 3D model simplification, computer-aided engineering, mechanical part retrieval, and assembly component identification. By integrating such a system, manufacturers can significantly enhance their machining processes and overall efficiency.
Limitations and Future Directions
While the proposed system achieves high accuracy in identifying machining processes and manufacturability, some limitations need to be addressed in future work. One notable limitation is the reliance on synthetic data, which may not fully capture the complexities of real-world scenarios. Additionally, the data preprocessing required for real-world applications can be time-consuming and labor-intensive.
Future research will focus on overcoming these limitations by incorporating real-world data and developing more efficient data preprocessing methods. Moreover, the system’s capabilities can be extended to recognize machining features from other data types, such as images and videos. We can further enhance the system’s applicability and robustness by addressing these challenges, paving the way for more advanced and intelligent manufacturing solutions.
Conclusion
Machining feature recognition through 3D models and machine learning is an efficient and accurate technology that can not only identify complex geometric features but also intelligently optimize traditional machining processes. Whether drilling, milling, or turning, deep learning models help manufacturers plan faster, improve product quality, and reduce costs.
In the future, with the continuous progress of artificial intelligence technology, the combination of 3D models and machine learning will bring a higher level of intelligence to the manufacturing industry, providing unprecedented support for complex processing.