What is the Manufacturing Scrap Rate?
Scrap rate measures the level of productivity in a manufacturing operation, which helps to determine the efficiency of the processes. A low scrap rate suggests that a production process is running smoothly and reducing costs; however, a high scrap rate could indicate that the organization is suffering from quality control problems or poor operating efficiency.
Manufacturing scrap analysis is crucial for calculating the scrap rate and understanding the total cost of scrap. By evaluating the ratio of unusable units to total units produced and applying dollar values to scrap parts, manufacturers can comprehensively understand various types of waste.
The rejection rate in the precision machining industry directly affects production efficiency, cost control, and customer satisfaction. Effective methods to reduce the scrap rate cannot only save material and labor costs but also improve overall production efficiency and product quality. The following practical tips will help you reduce the scrap rate and improve production efficiency in precision machining.
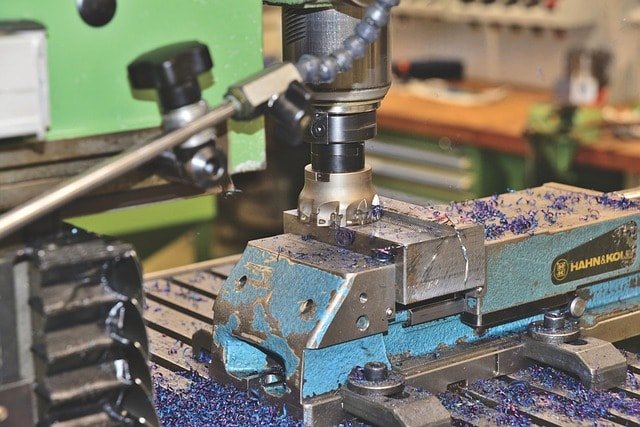
What Causes High Scrap Rates?
Various factors could contribute to a higher scrap rate, including:
1. Poor quality of raw materials
Poor quality or substandard raw materials are an essential factor leading to the rise in scrap rates. If the specifications or quality of raw materials are not up to standard, it will directly affect the quality of finished products. Monitoring scrap rate is essential in manufacturing to measure waste production and efficiency, and reducing excess scrap by using appropriate tools and techniques is crucial for maintaining high production quality. Utilizing specialized steel wire baskets can minimize damage to delicate parts and reduce scrap.
2. The device is aging or improperly maintained.
Insufficient accuracy of production equipment or long-term lack of maintenance will decrease processing accuracy. Equipment wear or failure can result in missized products, which in turn increases waste. Manufacturing scrap is inevitable within the production process, and understanding its common causes can help develop effective waste reduction strategies.
3. Unreasonable process design
If the production process design has problems, such as unreasonable process flow or unclear operation steps, it will increase production errors and the scrap rate.
4. Inadequate operator skills
The operator’s level and experience significantly impact the scrap rate. Inadequate operator skills, training, or operational errors can result in much waste in the production process.
5. Environmental factors
Conditions such as temperature, humidity, and cleanliness of the production environment may also affect product quality. For example, a temperature that is too high or too low may cause the material to deform, affecting the machining accuracy.

Streamline Manufacturing Processes for Efficiency
Streamlining the manufacturing process is crucial for reducing scrap rates and improving efficiency. Manufacturers can minimize scrap and maximize productivity by eliminating unnecessary steps and optimizing workflows. Here are some strategies to streamline manufacturing processes:
Process Standardization: Standardizing processes and procedures can help reduce variability and errors, often leading to scrap. By establishing clear guidelines and protocols, manufacturers can ensure that all employees follow the same procedures, reducing the risk of mistakes.
Automation: Automating specific processes can help reduce labor costs and minimize the risk of human error. By implementing automated systems, manufacturers can improve efficiency and reduce scrap rates, leading to a more streamlined production process.
Continuous Improvement: Encouraging a culture of continuous improvement can help manufacturers identify areas for enhancement and implement changes to reduce scrap rates. Manufacturers can foster a culture of ongoing optimization by empowering employees to suggest improvements and providing training and resources.
Improve Communication and Change Management
Effective communication and change management are pivotal in reducing scrap rates within manufacturing processes. When modifications are made to production processes or materials, recruits must communicate these changes clearly to all team members involved. This can be achieved through regular meetings, digital tools, and structured approaches to managing changes.
Implementing a robust change management process ensures that all team members are aware of changes and understand their roles in implementing them. This can include training programs, workshops, and feedback sessions to ensure everyone is on the same page. Good communication and change management can significantly reduce errors and defects in the production process. Manufacturers can minimize mistakes and enhance overall quality by ensuring that all team members are informed and understand their roles.
Moreover, effective communication and change management can improve labor and equipment utilization. Manufacturers can boost productivity and cut costs by streamlining production processes and reducing waste. This holistic approach not only aids in reducing scrap rates but also enhances the efficiency of the entire production process.
Another useful tip to reduce the scrap rate of precision machining
1. Strengthen process design and programming optimization
Process route design: Reasonable process design can effectively reduce unnecessary operation and complexity before processing. By optimizing the machining steps and reducing unnecessary process conversion, the potential source of error in machining can be reduced. Well-trained employees are crucial for optimizing processes to eliminate scrap effectively. A structured scrap reduction process can help identify and address the root causes of waste, leading to more efficient and cost-effective production.
Programming optimization: Proper programming is essential in CNC machining to reduce waste. Efficient programming not only improves machining accuracy but also reduces tool collisions, overcuts, or errors in cutting paths. Using advanced programming software for simulation, problems can be detected in advance, and waste products can be avoided in actual processing.
2. Select the appropriate tool and parameters.
Tool selection: Choosing the right tool for the workpiece material is critical to reducing scrap rates. Tools of different materials should be selected according to the workpiece’s hardness and processing requirements. For example, carbide tools are suitable for precision machining high-hardness materials, while high-speed steel tools are ideal for softer materials.
Optimization of cutting parameters: Adjusting cutting speed, feed speed, and cutting depth according to material characteristics can reduce workpiece surface defects and machining deformation. The correct cutting parameters ensure a longer tool life and reduce the scrap rate caused by tool wear. Effective labor and equipment utilization is crucial for continuous improvement initiatives, as both directly impact a company’s margins. The scrap rate formula is based on unusable units divided by the total units produced. At the same time, the first-pass yield focuses on the quality units produced divided by the total units produced. Understanding both metrics is essential for optimizing manufacturing efficiency.
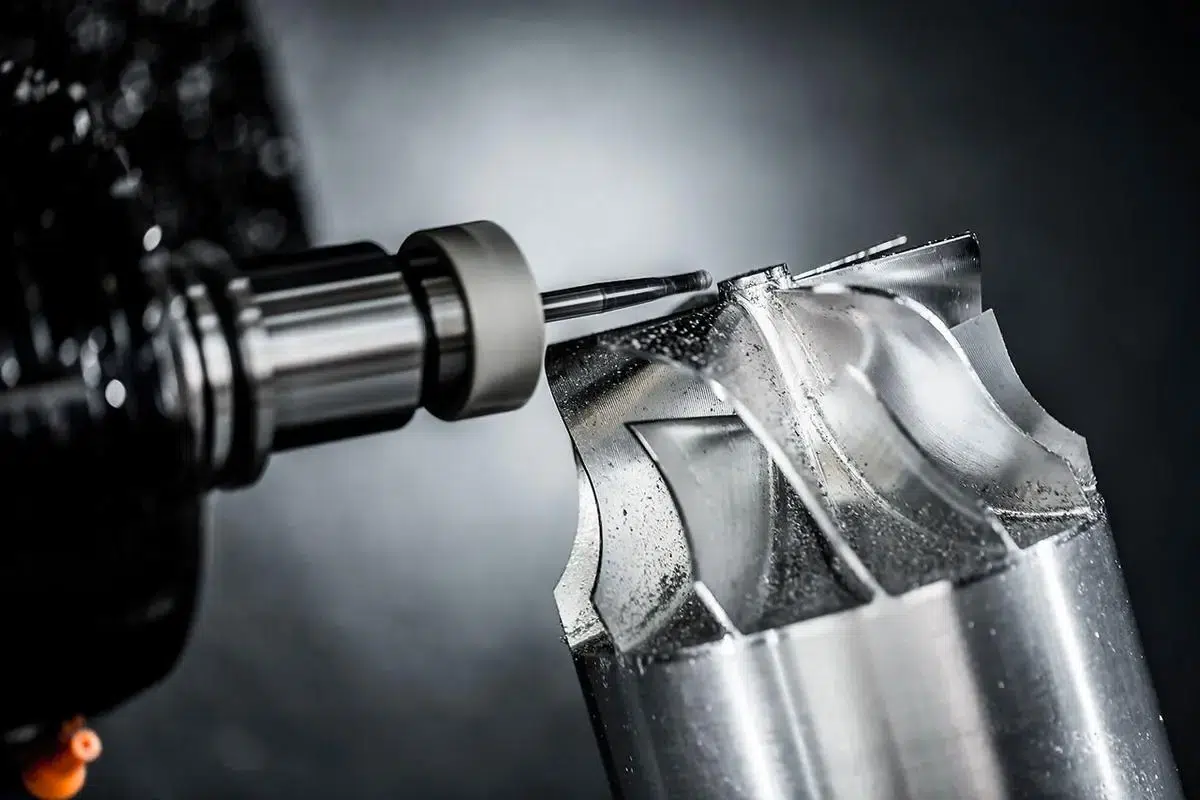
3. Maintain and calibrate the equipment regularly.
Equipment maintenance: Long-term use of the machine tool may lead to mechanical wear and loose moving parts, which will affect the processing accuracy and lead to waste. Regular maintenance and calibration of the machine ensure that it is maintained in optimal working condition and reduces waste caused by equipment failure.
Precision detection and calibration: Processing equipment and positioning accuracy will change during use, and regular calibration and detection can ensure that the equipment meets production requirements and avoids the accumulation of errors. High scrap rates can significantly affect profit margins, and methodologies like Lean and Six Sigma are effective strategies for identifying and addressing the factors contributing to scrap and rework.
4. Stability of workpiece clamping
Proper clamping method: Ensuring the stability of the workpiece during processing is essential to reduce the scrap rate. Selecting the appropriate fixture and ensuring that the workpiece is fixed firmly can avoid the processing errors caused by vibration and displacement. In addition, the use of custom fixtures can significantly improve the clamping accuracy.
Reduce the number of clamping: Each re-clamping will introduce errors, so the multiple clamping of the workpiece should be minimized. If multiple clamping must be performed, ensure the positioning is accurately repeated each time to reduce errors. Implementing scrap reduction techniques like Lean and Six Sigma can significantly lower waste and operational costs while improving overall process quality.
5. Process monitoring and real-time detection
Real-time monitoring of the machining process: By installing sensors or using machine vision systems to monitor the machining process in real time, problems such as tool wear and equipment vibration can be detected in time. Timely adjustment of processing parameters or stopping processing can effectively reduce the generation of waste products.
Process control feedback: Detection at each critical step of the process, combined with high-precision measuring equipment such as a coordinate measuring machine (CMM), allows precise monitoring of the workpiece size. With real-time feedback, it is possible to adjust the workpiece in time before it is out of alignment.
6. Training and operator skills upgrading
Skill training: The operator’s competency directly affects machining accuracy. Regular exercise can ensure operators can adequately use the equipment, read the drawings, and set the machining parameters, reducing the waste caused by improper operation.
Quality awareness: Encourage employees to maintain high-quality awareness during processing, carefully check process details, and pay attention to equipment operation, which can effectively reduce the scrap rate.
7. Environmental control: temperature and cleanliness
Temperature control: The temperature change in the processing environment will cause the thermal expansion and contraction of the workpiece, the tool, and the machine tool, resulting in unstable processing accuracy, especially in processing with high precision requirements. Therefore, maintaining a constant-temperature workshop is essential to reducing the scrap rate.
Keep the working environment clean: chips, dust, and lubricating oil residues can affect the quality and accuracy of the workpiece surface. Regular cleaning of the work area, tools, and machine tools can effectively reduce surface defects or errors in processing.

Review Material Sourcing
Reviewing material sourcing is an essential step in reducing scrap in manufacturing processes. Material sourcing involves evaluating the quality and reliability of raw materials and components.
Evaluate Material Quality: Evaluate the quality of raw materials and components to ensure they meet specifications. High-quality materials are less likely to contribute to scrap production.
Assess Supplier Reliability: to ensure they can deliver high-quality materials on time. Reliable suppliers are crucial for maintaining consistent production quality.
Negotiate with Suppliers: Negotiate with suppliers to improve material quality and reduce costs. Effective negotiation can lead to better material quality and cost savings.
Consider Alternative Materials: Consider alternative materials or suppliers to improve material quality and reduce costs. Exploring alternatives can provide better options for reducing scrap.
Implement a Material Inspection Process: To ensure materials meet specifications, implement a material inspection process. Regular inspections help identify and address material defects before they affect production.
Environmental Benefits of Scrap Reduction
Reducing scrap in manufacturing processes can have significant environmental benefits. By minimizing waste and improving efficiency, manufacturers can reduce their environmental impact and contribute to a more sustainable future.
Some environmental benefits of scrap reduction include reduced energy consumption, as minimizing waste and improving efficiency can lower energy use and carbon footprint. Additionally, reducing scrap can decrease water consumption, as many manufacturing processes require significant water. By improving efficiency, manufacturers can lower their water usage and environmental impact.
Furthermore, reducing scrap means less waste disposal, which helps lessen waste management’s mental impact and contributes to sustainability. Lastly, manufacturers can reduce their greenhouse gas emissions by cutting down on energy consumption and enhancing efficiency, further supporting a sustainable future. These environmental benefits underscore the importance of effective scrap reduction strategies in manufacturing processes.
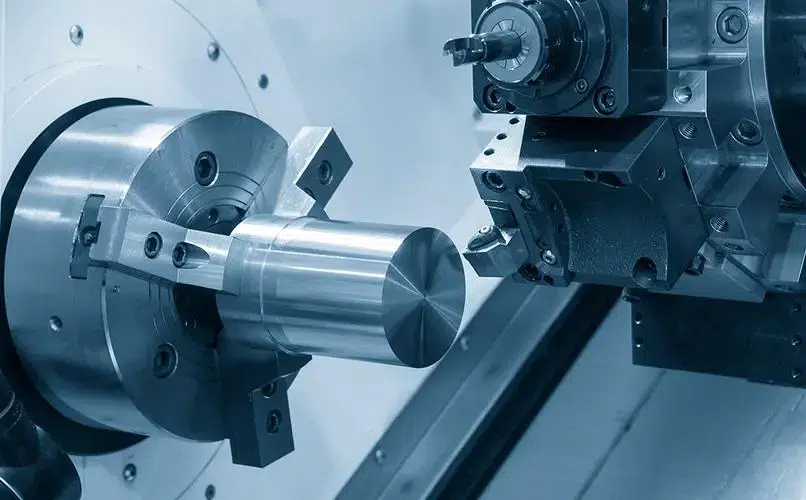
Conclusion
By strengthening process design and programming optimization, selecting the right tools, maintaining equipment regularly, improving clamping methods, monitoring the process in real time, and improving operator skills, companies can significantly reduce scrap rates and increase productivity. These tips help optimize the precision machining process, improve product quality, and enhance competitiveness.