Introduction
In the modern manufacturing industry, CNC machining has become a key technology that realizes the efficient and high-precision machining of various complex parts through computer-controlled precision machinery. A CNC machined part is critical as it involves factors that affect the machining process and costs, such as additional features like text or corner radii.
In the CNC machining process, the selection and control of the tool’s radius have a crucial impact on the machining quality, processing efficiency, and the final product’s performance. The use of different metal alloys, which can be enhanced through heat treatments, also plays a significant role in the properties and cost-effectiveness of CNC-machined parts. In this paper, the importance of radius in CNC machining will be discussed in detail, and its specific influence on different machining links and process parameters will be analyzed.
What is the radius in machining?
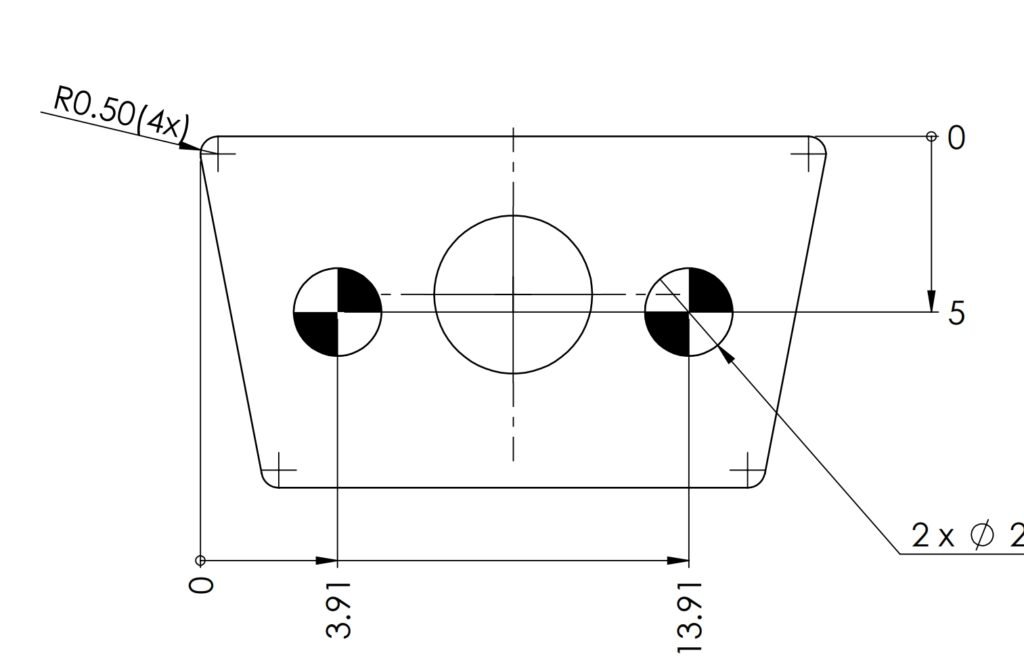
A machine operator’s radius determines how far he can travel if machining a machine tool. It also affects the quality of CNC machined parts that go out of the machines and the manufacturing time. The radius of CNC tools impacts the quality of the finished parts and production efficiency. Specifically, the radius in processing mainly includes the following aspects
Tool radius and tool path
Tool radius refers to the radius of the rounded corner or end of the tool used for cutting. Different types of knives and CNC milling tools have different radii, such as:
Rounded tool radius: A tool used for turning, milling, etc., whose tip is usually rounded rather than sharp to increase its strength and durability. Round-corner tools can reduce stress concentration during cutting and improve tool life and workpiece surface quality.
Ball tool radius: This tool is used for machining complex three-dimensional surfaces, especially in the processing of molds and aerospace parts. Ball tip tools provide a smoother cutting path for finishing and complex surface machining. Selecting the right cutting tool is crucial for achieving precise machining outcomes, as it directly affects part quality and productivity.
End mill radius: The end of the end mill usually has a radius to smooth the transition and reduce the cutting force. The radius design of the end mill helps improve the machined surface’s finish and reduce vibration during machining.
Different metal alloys respond uniquely to these tool radii, affecting their machinability, surface finish, and overall part quality.
Workpiece feature corner radius
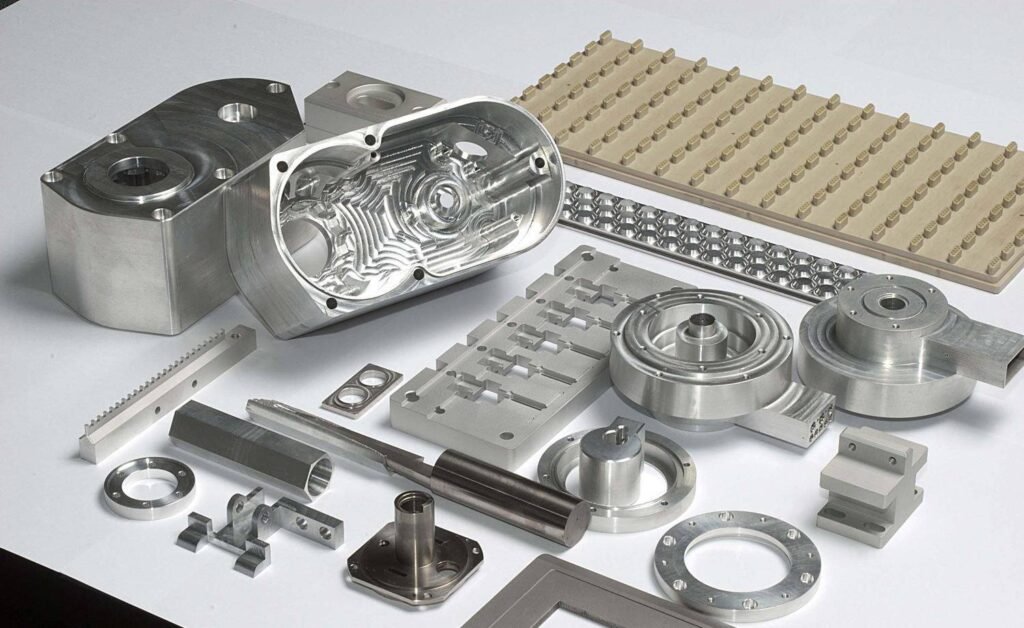
The feature radius of the workpiece refers to the radius of the rounded or chamfered corners of some specific parts of the workpiece. For example:
Inner Angle radius: At the inner corner of the workpiece, it is often designed to be rounded to reduce stress concentration and improve the structural strength of the workpiece. Sharp internal corners can pose challenges in CNC machining due to the geometry of cutting tools, making it difficult to achieve precise internal corners. The limited cutting length of CNC tools further complicates the machining of sharp internal corners, as tools are optimized for specific dimensional limits. The inner angular radius can effectively disperse the stress and avoid cracks or fractures in the workpiece during use.
Outer corner radius: The rounded corner design at the outer corner of the workpiece can reduce edge wear and improve surface quality and aesthetics. A reasonable design of the outer Angle radius helps to improve the workpiece’s durability and appearance quality.
Aperture radius: In drilling, reaming, and other operations, the hole’s edge may need to be chamfered or rounded to facilitate assembly and use. The design of the aperture radius can improve assembly accuracy and reduce wear and stress concentration during assembly. Machining internal features such as intersecting holes or cavities can be
Surface radius
Surface radius refers to the radius of the specific curvature of the workpiece surface, especially when machining complex three-dimensional surfaces. For example:
Convex radius: The radius of the surface in the convex part of the workpiece, which usually requires fine machining with a ball tool. The cylindrical shape of the milling tool creates a natural radius when cutting corners, thus influencing the efficiency and quality of the machining process and the final surface finish of the part. The design of a convex surface radius can improve the aesthetics and functionality of the workpiece.
Concave surface radius: The radius of the surface in the concave part of the workpiece also needs to be achieved by a specific tool and machining path. A reasonable choice of the concave surface radius helps improve machining accuracy and surface quality. Using larger corner radii can enhance machining efficiency and surface finish quality, as larger tools can achieve these radii while operating faster, reducing machining time and costs.
Different metal alloys require specific surface radii for optimal machining, as the physical properties of materials like Aluminum 6061, Stainless Steel 303, and Brass C360 influence the choice of tools and machining parameters.
Why are sharp corners an issue in CNC machining?
It determines how many corner points a machining tool uses during a machine tool production. This can be directly affected if parts are taken off/ removed from the machine, or if there is longer production time. The minimum inner edge radius available on CNC is the tool’s radius. If we want our corners sharp and pristine, our tools will have to follow this 180-degree path, and CNC machines do not have the tools to do the same. You will have to stop your machine to move the pieces.
Different metal alloys handle sharp corners differently in CNC machining, with some materials like Aluminum 6061, Stainless Steel 303, and Brass C360 offering better machinability and precision.
1. Machining accuracy and details
Sharp corners can improve machining detail and accuracy on some workpieces. Especially in producing micro-machining and high-precision parts, sharp angles enable complex geometrics and fine features. For example:
Fine parts: When machining fine parts such as precision instruments and electronic components, sharp corners can achieve higher machining accuracy and detail and can also be used for machining small holes and slits.
Complex contour: In some complex contour and pattern processing, sharp corners can ensure fine cutting and contour accuracy, especially in mold-making and engraving areas.
The properties of different metal alloys, such as Aluminum 6061, Stainless Steel 303, and Brass C360, can significantly affect machining accuracy and details.
2. Cutting speed and efficiency
In some cases, sharp-angle tools can improve cutting speed and processing efficiency. Due to the geometric properties of sharp-angle tools, they can cut into the material more quickly, reducing cutting resistance. For example:
High-speed cutting: In high-speed cutting applications, sharp-angle tools can improve material removal rates, thereby speeding up the processing speed, suitable for mass production and efficient processing scenarios.
Material penetration: Sharp-angle tools are excellent at drilling and penetrating cutting, which can quickly penetrate materials and reduce processing time.
Additionally, the properties of different metal alloys, such as Aluminum 6061, Stainless Steel 303, and Brass C360, can significantly affect cutting speed and efficiency.
3. Tool selection and design
In CNC machining, the choice and design of the tool are very important for sharp corner machining. Different types of sharp corner tools are suitable for different machining tasks and materials:
V-shaped tool: This tool has a sharp Angle and is suitable for machining tasks such as engraving and lettering that require high precision and detail.
Bit Angle: The design of the bit Angle ensures the accuracy and efficiency of the drilling, especially in the processing of hard materials.
The properties of different metal alloys, such as hardness and machinability, significantly affect tool selection and design.
Why tool radius compensation is important when creating a CNC part Programme?
In this case, the correct position of the machining tool may not ensure the piece’s cleanliness, as a larger hole exists between the cutting edge and the tool’s workpiece surfaces. You will also need a CNC mill to adjust the tool radius for this gap to provide maximum finishing. Tool radius compensation is crucial for machining different metal alloys, ensuring the final product’s precision and quality.
1. Improve machining accuracy
In CNC machining, there may be deviations between the actual cutting path and the theoretical path, mainly due to the influence of the tool radius. Through the tool radius compensation, the cutting path of the tool can be precisely controlled to ensure that the size and geometry of the part meet the design requirements. The properties of different metal alloys, such as hardness and machinability, also play a crucial role in achieving machining accuracy. For example:
Precise profile machining: When machining complex profiles and surfaces, tool radius compensation can ensure that the cutting path accurately fits the design curve and avoids machining errors.
High-precision hole machining: During drilling and boring, the tool radius compensation can ensure the accuracy of the aperture and position.
2. Enhance programming efficiency
Tool radius compensation makes programming simpler and more flexible, reducing the risk of manual calculations and programming errors:
Simplify the programming process: Programmers only need to program according to the geometry of the part without considering the specific radius of the tool. The CNC system automatically processes the tool radius compensation, improving programming efficiency.
Reduce manual adjustment: When replacing the tool or using a tool with a different radius, there is no need to rewrite the machining program; only the compensation parameters need to be adjusted, saving programming time.
Additionally, the properties of different metal alloys, such as Aluminum 6061, Stainless Steel 303, and Brass C360, can significantly affect programming efficiency by influencing factors like hardness, strength, and machinability.
3. Provide processing flexibility
Tool radius compensation allows flexible adjustment of cutting parameters and tools during machining to suit different machining needs and conditions:
Easy tool replacement: When using a tool with a different radius or replacing a new tool after tool wear, you only need to adjust the compensation value without modifying the entire procedure.
Adapt to diversified processing: When processing a variety of parts, you can adjust the tool radius compensation parameters to flexibly respond to different processing requirements and improve production efficiency.
The properties of different metal alloys, such as Aluminum 6061, Stainless Steel 303, and Brass C360, also affect processing flexibility by influencing hardness, strength, and machinability.
4. Manage tool wear
The tool will gradually wear out during use, affecting the cutting accuracy. Tool radius compensation can help manage and compensate for tool wear:
Wear compensation: After the tool wears, you can adjust the compensation parameters to continue using it without affecting the machining accuracy and extend its service life.
Periodic adjustment: Compensation parameters are regularly adjusted according to tool wear to ensure that each machining can achieve the expected accuracy and quality.
The properties of different metal alloys, such as hardness and strength, significantly influence tool wear. Harder alloys typically cause more rapid wear.
5. Reduce processing errors
Tool radius compensation can effectively reduce machining errors, especially in the machining of complex shapes and tight tolerances:
Avoid path deviation: Tool radius compensation can avoid path deviation due to tool radius, ensuring that the cutting path precisely matches the design path.
Improve consistency: By compensating the tool radius, ensure the processing consistency of each part to meet the high precision requirements of mass production.
Additionally, the properties of different metal alloys, such as hardness and machinability, can significantly affect processing errors.
6. Improve surface quality
Tool radius compensation helps optimize cutting conditions and improve part surface quality:
Smooth cutting path: Improve surface finish by precisely controlling the tool path to reduce vibration and tool run-out during cutting.
Reduce machining: Reduce machining errors through tool radius compensation, reduce the need for machining and finishing, and improve production efficiency and surface quality.
The properties of different metal alloys, such as Aluminum 6061, Stainless Steel 303, and Brass C360, can significantly affect the surface quality of CNC-machined parts.
The importance of stress distribution and structural strength
The selection and design of the radius have a crucial effect on the stress distribution and structural strength of the workpiece. Reasonable radius design can improve the fatigue resistance and service life of the workpiece and significantly improve its mechanical properties and safety. The importance of radius in CNC machining is analyzed from the point of view of stress distribution and structural strength.
1. Stress concentration effect
Stress concentration refers to the phenomenon of stress concentration in certain areas of the workpiece due to sudden changes or discontinuities in the geometry. Sharp corners, edges, and geometric changes often create stress concentrations that can lead to fatigue failure or material fracture. Introducing an appropriate radius can significantly reduce the stress concentration effect, disperse the stress, and improve the structural strength of the workpiece. For example:
Inner corner rounded design: By designing an appropriate rounded radius at the inner corner of the workpiece, the stress can be effectively dispersed and the stress concentration can be avoided. The design of the inner corner radius is particularly important because stress concentration at the inner corner can lead to fatigue cracks in the material.
Transition fillet: In areas with sharp changes in geometry, introducing a transition fillet can smooth the stress distribution and reduce the stress concentration effect. For example, in parts such as bearing housings, connecting arms, and brackets, the design of transition fillets helps to improve the fatigue life and reliability of parts.
2. Improve fatigue resistance
The workpiece is often subjected to periodic load during use, resulting in fatigue failure. A reasonable radius design can significantly improve the fatigue resistance of the workpiece. For example:
Fatigue life extension: Introducing a suitable rounded radius in the design can reduce stress concentration and extend the fatigue life of the workpiece. For example, in aircraft structural parts and automobile parts, the service life of the parts can be effectively extended through the rounded corner design.
Fatigue crack control: By optimizing the radius design, the initiation and propagation of fatigue cracks can be controlled. For example, in welded joints and frame structures, rounded corner designs can reduce the risk of fatigue cracks and improve the reliability of the overall structure.
3. Improvement of structural strength and stiffness
A reasonable radius design can improve the workpiece’s overall structural strength and stiffness. For example:
Uniform strength distribution: the rounded radius can make the load evenly distributed on the workpiece, avoid local stress being too high, and improve the overall strength of the workpiece. For example, in mechanical transmission parts, a reasonably rounded corner design can improve the bearing capacity of parts.
Stiffness enhancement: By introducing a suitable radius design, the stiffness of the workpiece can be improved, and the deformation can be reduced. For example, in structural parts and support parts, a rounded corner design can improve the flexural and torsional stiffness of parts and increase the stability of the structure.
4. Optimization of processing quality and process performance
The reasonable design of the radius not only affects the mechanical properties of the workpiece but also has an important impact on the machining quality and process properties. For example:
Machining stability: The proper rounded corner design can improve the machining stability of the tool, reduce the vibration and stress concentration generated during the cutting process, and improve the quality of the machined surface.
Process simplification: By optimizing the radius design, the processing process can be simplified and efficiency improved. For example, in-mold processing and complex parts manufacturing, a reasonably rounded corner design can reduce processing steps and improve production efficiency.
Optimizing processing quality and process performance is crucial for CNC machined parts, as it helps balance quality and cost-effectiveness.
Conclusion
In summary, the radius plays an important role in CNC machining. By reasonable selection and control of tool radius, machining accuracy, efficiency, and surface quality can be significantly improved, tool life can be extended, processing costs can be reduced, and the workpiece’s stress distribution and structural strength can be optimized. CNC machined parts are critical in this context as additional features like text or corner radii can impact the complexity and cost, guiding designers to balance quality and cost-effectiveness.
Therefore, in the CNC machining process, the influence of the radius must be fully considered, and the tool and processing parameters must be scientifically selected to achieve efficient and high-quality machining goals. This can meet the high standards of industrial production and bring significant economic benefits and competitive advantages to enterprises. Additionally, the choice of metal alloys and their heat treatments can enhance the physical properties of CNC-machined parts, affecting hardness, strength, and machinability, which are crucial for cost-effective manufacturing.